What happens if China restricts rare earths supply ?
Forum rules
Don't poop in these threads. This isn't Europe, okay? There are rules here!
Don't poop in these threads. This isn't Europe, okay? There are rules here!
- BigP
- Posts: 4970
- Joined: Mon Mar 19, 2018 3:56 pm
Re: What happens if China restricts rare earths supply ?
Rare earth elements facts
Rare earth elements (REEs) are a group of 15 elements referred to as the lanthanide series in the periodic table of elements. Scandium and yttrium, while not true REEs, are also included in this categorization because they exhibit similar properties to the lanthanides and are always found in the same ore bodies. REEs are key components in many electronic devices that we use in our daily lives, as well as in a variety of industrial applications.
Key facts
Canada has some of the largest known reserves and resources (measured and indicated) of rare earths in the world, estimated at over 15 million tonnes of rare earth oxides.
China is the world’s largest producer of REEs, accounting for over 70% of global annual production, estimated at 120,000 tonnes in 2018.
Learn more about rare earth elements
Uses
Production
International context
Uses
Rare earth elements (REEs) are used in a variety of industrial applications, including electronics, clean energy, aerospace, automotive and defence.
The manufacturing of magnets represents the single largest and most important end use for REEs, accounting for 21% of total consumption.
Permanent magnets are an essential component of modern electronics used in cell phones, televisions, computers, automobiles, wind turbines, jet aircraft and many other products. REEs are also widely used in high-technology and “green” products because of their luminescent and catalytic properties.
Rare earth elements uses, 2018
Text version
Production
While not a current producer of REEs, Canada is host to a number of advanced exploration projects and some of the largest reserves and resources (measured and indicated) of these metals, estimated at over 15 million tonnes of rare earth oxides.
REEs are categorized as being either “light” or “heavy”:
Light REEs (lanthanum, cerium, praseodymium, neodymium, promethium, samarium, europium, gadolinium and scandium) are produced in global abundance and are in surplus supply
Heavy REEs (terbium, dysprosium, holmium, erbium, thulium, ytterbium, lutetium and yttrium) are produced mainly in China and are in limited supply. Global efforts to bring new resources to the marketplace continue.
Many of Canada’s most advanced REEs exploration projects contain high concentrations of the globally valued heavy REEs used in high-technology and clean-energy applications.
Learn more about why rare earth elements are important.
International context
China is the world’s largest producer of REEs, accounting for over 70% of global annual production, estimated at 120,000 tonnes for 2018. The remaining 30% is mostly shared among five other countries: Australia, United States, Myanmar, Russia and India. China remains virtually the only producer of the valued heavy REEs.
World production of REEs, by country, 2018 (p)
Ranking Country Thousand tonnes Percentage of total
1 China 120.0 70.6%
2 Australia 20.0 11.8%
3 United States 15.0 8.8%
4 Myanmar 5.0 2.9%
5 Russia 2.6 1.5%
- Other countries 7.4 4.4%
- Total 170 100.0%
The United States was the world’s largest supplier of REEs until the emergence of China in the mid-1990s. China was virtually the world’s sole REEs supplier until 2012, when the now-bankrupt US producer Molycorp Inc. and the Australian company Lynas Corporation Ltd. commenced commercial production.
World REEs production, 1988–2018 (p)
Text version
Notes and sources
Rare earth elements (REEs) are a group of 15 elements referred to as the lanthanide series in the periodic table of elements. Scandium and yttrium, while not true REEs, are also included in this categorization because they exhibit similar properties to the lanthanides and are always found in the same ore bodies. REEs are key components in many electronic devices that we use in our daily lives, as well as in a variety of industrial applications.
Key facts
Canada has some of the largest known reserves and resources (measured and indicated) of rare earths in the world, estimated at over 15 million tonnes of rare earth oxides.
China is the world’s largest producer of REEs, accounting for over 70% of global annual production, estimated at 120,000 tonnes in 2018.
Learn more about rare earth elements
Uses
Production
International context
Uses
Rare earth elements (REEs) are used in a variety of industrial applications, including electronics, clean energy, aerospace, automotive and defence.
The manufacturing of magnets represents the single largest and most important end use for REEs, accounting for 21% of total consumption.
Permanent magnets are an essential component of modern electronics used in cell phones, televisions, computers, automobiles, wind turbines, jet aircraft and many other products. REEs are also widely used in high-technology and “green” products because of their luminescent and catalytic properties.
Rare earth elements uses, 2018
Text version
Production
While not a current producer of REEs, Canada is host to a number of advanced exploration projects and some of the largest reserves and resources (measured and indicated) of these metals, estimated at over 15 million tonnes of rare earth oxides.
REEs are categorized as being either “light” or “heavy”:
Light REEs (lanthanum, cerium, praseodymium, neodymium, promethium, samarium, europium, gadolinium and scandium) are produced in global abundance and are in surplus supply
Heavy REEs (terbium, dysprosium, holmium, erbium, thulium, ytterbium, lutetium and yttrium) are produced mainly in China and are in limited supply. Global efforts to bring new resources to the marketplace continue.
Many of Canada’s most advanced REEs exploration projects contain high concentrations of the globally valued heavy REEs used in high-technology and clean-energy applications.
Learn more about why rare earth elements are important.
International context
China is the world’s largest producer of REEs, accounting for over 70% of global annual production, estimated at 120,000 tonnes for 2018. The remaining 30% is mostly shared among five other countries: Australia, United States, Myanmar, Russia and India. China remains virtually the only producer of the valued heavy REEs.
World production of REEs, by country, 2018 (p)
Ranking Country Thousand tonnes Percentage of total
1 China 120.0 70.6%
2 Australia 20.0 11.8%
3 United States 15.0 8.8%
4 Myanmar 5.0 2.9%
5 Russia 2.6 1.5%
- Other countries 7.4 4.4%
- Total 170 100.0%
The United States was the world’s largest supplier of REEs until the emergence of China in the mid-1990s. China was virtually the world’s sole REEs supplier until 2012, when the now-bankrupt US producer Molycorp Inc. and the Australian company Lynas Corporation Ltd. commenced commercial production.
World REEs production, 1988–2018 (p)
Text version
Notes and sources
- BigP
- Posts: 4970
- Joined: Mon Mar 19, 2018 3:56 pm
Re: What happens if China restricts rare earths supply ?
..........................................HOLY SHIT!! My IQ just suddenly quadrupled I must almost be as smart as Julie and his pet pig ..
- BigP
- Posts: 4970
- Joined: Mon Mar 19, 2018 3:56 pm
Re: What happens if China restricts rare earths supply ?
Rare-earth element
WRITTEN BY: Karl A. Gschneidner, Jr.Vitalij K. Pecharsky
See Article History
Alternative Titles: inner transition element, rare-earth metal
Rare-earth element, any member of the group of chemical elements consisting of three elements in Group 3 (scandium [Sc], yttrium [Y], and lanthanum [La]) and the first extended row of elements below the main body of the periodic table (cerium [Ce] through lutetium [Lu]). The elements cerium through lutetium are called the lanthanides, but many scientists also, though incorrectly, call those elements rare earths.
The rare earths are generally trivalent elements, but a few have other valences. Cerium, praseodymium, and terbium can be tetravalent; samarium, europium and ytterbium, on the other hand, can be divalent. Many introductory science books view the rare earths as being so chemically similar to one another that collectively they can be considered as one element. To a certain degree that is correct—about 25 percent of their uses are based on this close similarity—but the other 75 percent of rare-earth usage is based on the unique properties of the individual elements. Furthermore, a close examination of these elements reveals vast differences in their behaviours and properties; e.g., the melting point of lanthanum, the prototype element of the lanthanide series (918 °C, or 1,684 °F), is much lower than the melting point of lutetium, the last element in the series (1,663 °C, or 3,025 °F). This difference is much larger than that found in many groups of the periodic table; e.g., the melting points of copper, silver, and gold vary by only about 100 °C (180 °F).
The name rare earths itself is a misnomer. At the time of their discovery in the 18th century, they were found to be a component of complex oxides, which were called “earths” at that time. Furthermore, these minerals seemed to be scarce, and thus these newly discovered elements were named “rare earths.” Actually, these elements are quite abundant and exist in many workable deposits throughout the world. The 16 naturally occurring rare earths fall into the 50th percentile of elemental abundances. By the early 21st century, China had become the world’s largest producer of rare-earth elements. Australia, Brazil, India, Kazakhstan, Malaysia, Russia, South Africa, and the United States also extract and refine significant quantities of these materials.
00:00
02:17
Many people do not realize the enormous impact the rare-earth elements have on their daily lives, but it is almost impossible to avoid a piece of modern technology that does not contain any. Even a product as simple as a lighter flint contains rare-earth elements. Their pervasiveness is exemplified by the modern automobile, one of the biggest consumers of rare-earth products. Dozens of electric motors in a typical automobile, as well as the speakers of its sound system, use neodymium-iron-boron permanent magnets. Electrical sensors employ yttria-stabilized zirconia to measure and control the oxygen content of the fuel. The three-way catalytic converter relies on cerium oxides to reduce nitrogen oxides to nitrogen gas and oxidize carbon monoxide to carbon dioxide and unburned hydrocarbons to carbon dioxide and water in the exhaust products. Phosphors in optical displays contain yttrium, europium, and terbium oxides. The windshield, mirrors, and lenses are polished using cerium oxides. Even the gasoline or diesel fuel that propels the vehicle was refined using rare-earth cracking catalysts containing lanthanum, cerium, or mixed-rare-earth oxides. Hybrid automobiles are powered by a nickel–lanthanum metal hydride rechargeable battery and an electrical traction motor, with permanent magnets containing rare-earth elements. In addition, modern media and communication devices—cell phones, televisions, and computers—all employ rare earths as magnets for speakers and hard drives and phosphors for optical displays. The amounts of rare earths used are quite small (0.1–5 percent by weight, except for permanent magnets, which contain about 25 percent neodymium), but they are critical, and any of those devices would not work as well, or would be significantly heavier, if it were not for the rare earths.
Get unlimited ad-free access to all Britannica’s trusted content.
Subscribe Today
Discovery And History
Although the rare earths have been around since the formation of Earth, their existence did not come to light until the late 18th century. In 1787 the Swedish army lieutenant Carl Axel Arrhenius discovered a unique black mineral in a small quarry in Ytterby (a small town near Stockholm). That mineral was a mixture of rare earths, and the first individual element to be isolated was cerium in 1803.
The history of the individual rare-earth elements is both complex and confused, mainly because of their chemical similarity. Many “newly discovered elements” were not one element but mixtures of as many as six different rare-earth elements. Furthermore, there were claims of discovery of a large number of other “elements,” which were supposed to be members of the rare-earth series but were not.
The last naturally occurring rare-earth element (lutetium) was discovered in 1907, but research into the chemistry of these elements was difficult because no one knew how many true rare-earth elements existed. Fortunately, in 1913–14 the research of Danish physicist Niels Bohr and English physicist Henry Gwyn Jeffreys Moseley resolved this situation. Bohr’s theory of the hydrogen atom enabled theoreticians to show that only 14 lanthanides exist. Moseley’s experimental studies verified the existence of 13 of these elements and showed that the 14th lanthanide must be element 61 and lie between neodymium and samarium.
In the 1920s the search for element 61 was intense. In 1926 groups of scientists at the University of Florence, Italy, and at the University of Illinois claimed to have discovered element 61 and named the element florentium and illinium, respectively, but their claims could not be independently verified. The furor of these claims and counterclaims eventually died down by 1930. It was not until 1947, after the fission of uranium, that element 61 definitely was isolated and named promethium by scientists at the U.S. Atomic Energy Commission’s Oak Ridge National Laboratory in Tennessee. (More details about the discovery of the individual elements are found in the articles about those elements.)
During the 160 years of discovery (1787–1947), the separation and purification of the rare-earth elements was a difficult and time-consuming process. Many scientists spent their whole lives attempting to obtain a 99 percent pure rare earth, usually by fractional crystallization, which makes use of the slight differences of the solubility of a rare-earth salt in an aqueous solution compared with that of a neighbouring lanthanide element.
Because the rare-earth elements were found to be fission products of the splitting of a uranium atom, the U.S. Atomic Energy Commission made a great effort to develop new methods for separating the rare-earth elements. However, in 1947 Gerald E. Boyd and colleagues at Oak Ridge National Laboratory and Frank Harold Spedding and colleagues at the Ames Laboratory in Iowa simultaneously published results which showed that ion-exchange processes offered a much better way for separating the rare earths.
SpaceNext50
Rare-earth element
KEY PEOPLE
Frank Harold Spedding
Carl Gustaf Mosander
RELATED TOPICS
Chemical element
Transition metal
Actinoid element
Gadolinium
Cerium
Lanthanum
Samarium
Neodymium
Ytterbium
Scandium
Abundance, Occurrence, And Reserves
As noted above, the rare earths are fairly abundant, but their availability is somewhat limited, primarily because their concentration levels in many ores are quite low (less than 5 percent by weight). An economically viable source should contain more than 5 percent rare earths, unless they are mined with another product—e.g., zirconium, uranium, or iron—which allows economic recovery of ore bodies with concentrations of as little as 0.5 percent by weight.
Of the 83 naturally occurring elements, the 16 naturally occurring rare-earth elements fall into the 50th percentile of the elemental abundances. Promethium, which is radioactive, with the most stable isotope having a half-life of 17.7 years, is not considered to be naturally occurring, although trace amounts have been found in some radioactive ores. Cerium, which is the most abundant, ranks 28th, and thulium, the least abundant, ranks 63rd. Collectively, the rare earths rank as the 22nd most abundant “element” (at the 68th percentile mark). The non-lanthanide rare-earth elements, yttrium and scandium, are 29th and 44th, respectively, in their abundances.
Lanthanum and the light lanthanides (cerium through europium) are more abundant than the heavy lanthanides (gadolinium through lutetium). Thus, the individual light lanthanide elements are generally less expensive than the heavy lanthanide elements. Furthermore, the metals with even atomic numbers (cerium, neodymium, samarium, gadolinium, dysprosium, erbium, and ytterbium) are more abundant than their neighbours with odd atomic numbers (lanthanum, praseodymium, promethium, europium, terbium, holmium, thulium, and lutetium).
Rare-earth ore deposits are found all over the world. The major ores are in China, the United States, Australia, and Russia, while other viable ore bodies are found in Canada, India, South Africa, and southeast Asia. The major minerals contained in these ore bodies are bastnasite (fluorocarbonate), monazite (phosphate), loparite [(R,Na,Sr,Ca)(Ti,Nb,Ta,Fe3+)O3], and laterite clays (SiO2, Al2O3, and Fe2O3).
Chinese deposits accounted for about 80 percent of the rare earths mined in the world in 2017 (105,000 tons of rare-earth oxide). About 94 percent of the rare earths mined in China are from bastnasite deposits. The major deposit is located at Bayan Obo, Inner Mongolia (83 percent), while smaller deposits are mined in Shandong (8 percent) and Sichuan (3 percent) provinces. About 3 percent comes from laterite (ion absorption) clays located in Jiangxi and Guangdong provinces in southern China, while the remaining 3 percent is produced at a variety of locations.
Officially, 130,000 metric tons of REO equivalent was mined in 2017, but a black market in rare earths was said to produce an additional 25 percent of that amount. Most black-market rare-earth materials are smuggled out of China.
China’s monopoly allowed it to raise prices by hundreds of percent for various rare-earth materials from 2009 to 2011 and also to impose export quotas on many of these products. This brought about a large change in the dynamics of the rare-earth markets. Mining of bastnasite resumed at Mountain Pass, California, in 2011 after a nine-year hiatus, and mining of monazite began that same year at Mount Weld, Australia. At the same time, loparite was being mined in Russia, while monazite was mined in India, Vietnam, Thailand, and Malaysia. Those and other mining operations brought a new equilibrium between demand and supply in which China was still the major supplier of rare-earth minerals, but companies either sought alternative sources, used less, or recycled more rare earths.
As of 2017, known world reserves of rare-earth minerals amounted to some 120 million metric tons of contained REO. China has the largest fraction (37 percent), followed by Brazil and Vietnam (18 percent each), Russia (15 percent), and the remaining countries (12 percent). With reserves this large, the world would not run out of rare earths for more than 900 years if demand for the minerals would remain at 2017 levels. Historically, however, demand for rare earths has risen at a rate of about 10 percent per year. If demand continued to grow at this rate and no recycling of produced rare earths were undertaken, known world reserves likely would be exhausted sometime after the mid-21st century.
Considering both the limited reserves and high value of the rare-earth metals, recycling these elements from consumer products that reach the end of their useful life is expected to become more important. At present, only scrap metal, magnet materials, and compounds used in the manufacture of phosphors and catalysts are recycled. However, products that contain relatively large amounts of rare earths could be recycled immediately using existing techniques. These include rechargeable nickel–metal hydride batteries that contain a few grams to a few kilograms of LaNi5-based alloys as a hydrogen absorber as well as large SmCo5- and Nd2Fe14B-based permanent magnets. All of these materials hold 25–30 percent by weight light lanthanides—much more than even the best rare-earth-containing ore (see below). However, the majority of consumer electronic devices contain only small amounts of rare earths. For example, a hard drive’s spindle magnet contains only a few grams of Nd2Fe14B. A speaker magnet of a cellular phone makes up less than 0.1 percent of the total mass of the telephone. A compact fluorescent lamp has only a fraction of a gram of lanthanide metals in the phosphor. Considering the complexity of many modern electronic devices, recycling of rare earths must be done simultaneously with recycling of other valuable resources and potentially dangerous substances. These include precious metals (such as silver, gold, and palladium), nonferrous metals (such as aluminum, cobalt, nickel, copper, gallium, and zinc), carcinogens (such as cadmium), poisons (such as mercury, lead, and beryllium), plastics, glass, and ceramics. Numerous scientific and engineering issues, therefore, must be resolved, first, in order to create consumer products that are easily recyclable at the end of their life and, second, to make recycling of rare earths both meaningful and economical, thus making the best use of the rare earths—an extremely valuable but limited resource provided by nature.
SpaceNext50
SIMILAR TOPICS
Hydrogen
Alkali metal
Alkaline-earth metal
Carbon group element
Boron group element
Oxygen group element
Nitrogen group element
Halogen
Noble gas
Zinc group element
Minerals And Ores
The content of the individual rare-earth elements varies considerably from mineral to mineral and from deposit to deposit. The minerals and ores are generally classified as “light” or “heavy”; in the former group most of the elements present are the light-atomic-weight elements (i.e., lanthanum, cerium, praseodymium, neodymium, samarium, and europium), whereas most of the elements in the latter group are the heavy-atomic-weight elements (i.e., gadolinium, terbium, dysprosium, holmium, erbium, thulium, ytterbium, and lutetium, plus yttrium, which is considered to be a member of the heavy group because it is found in the ores with the heavy lanthanides). The geochemistry of scandium is significantly different from the geochemistry of the other rare-earth elements. Information on its ores and minerals is provided in the article scandium. Essentially no scandium is found in any of the minerals discussed below.
Of the approximately 160 minerals that are known to contain rare earths, only four are currently mined for their rare earths: bastnasite, laterite clays, monazite, and loparite. With the exception of laterite clays, these minerals are good sources of light lanthanides and lanthanum and account for about 95 percent of the rare earths in use. Laterite clays are a commercial source of the heavy lanthanides and yttrium.
Other minerals that have been used as a source of rare earths are apatite, euxenite, gadolinite, and xenotime. Allanite, fluorite, perovskite, sphene, and zircon have the potential to be future sources of rare earths. (In addition, uranium and iron tailings have been used in the past as a source of the heavy lanthanides plus yttrium and of the light lanthanides plus lanthanum, respectively.) Many of these minerals such as apatite and euxenite are processed for other constituents, and the rare earths could be extracted as a by-product. In addition to minerals found in Earth’s crust, there are some deep-sea muds, such as those near Minamitori Island, Japan, that contain rare-earth elements. The concentrations vary from hundreds to thousands of parts per million, and these muds may one day be a source of rare earths.
The idealized chemical compositions of these 13 minerals that are sources of rare earths are given in the table.
Composition of selected rare-earth minerals
name idealized composition primary rare-earth content
allanite (Ca,Fe2+)(R,Al,Fe3+)3Si3O13H R = light lanthanoids
apatite Ca5(PO4)3F R = light lanthanoids
bastnasite RCO3F R = light lanthanoids (60–70%)
euxenite R(Nb,Ta)TiO6 ∙ xH2O R = heavy lanthanoids plus Y (15–43%)
fluorite CaF2 R = heavy lanthanoids plus Y
gadolinite R2(Fe2+,Be)3Si2O10 R = heavy lanthanoids plus Y (34–65%)
laterite clays SiO2, Al2O3, Fe2O3 R = heavy lanthanoids plus Y
loparite (R,Na,Sr,Ca)(Ti,Nb,Ta,Fe3+)O3 R = light lanthanoids (32–34%)
monazite RPO4 R = light lanthanoids (50–78%)
perovskite CaTiO3 R = light lanthanoids
sphene CaTiSiO4X2 (X = ½O2−, OH−, or F−) R = light lanthanoids
xenotime RPO4 R = heavy lanthanoids plus Y (54–65%)
zircon ZrSiO2 R = both light and heavy lanthanoids plus Y
Bastnasite
Bastnasite, a fluorocarbonate, is the principal source of rare earths. About 94 percent of the rare earths used in the world come from mines in Mountain Pass, California, U.S.; Bayan Obo, Inner Mongolia, China; Shandong province, China; and Sichuan province, China. The Bayan Obo deposit is slightly richer in praseodymium and neodymium than the Mountain Pass bastnasite is, primarily at the expense of the lanthanum content, which is 10 percent greater in the Mountain Pass ore. The rare-earth contents of the Shandong and Sichuan minerals are slightly different from that of the Bayan Obo minerals and also from each other’s. The Shandong bastnasite is similar to the Mountain Pass mineral. The Sichuan ore has more lanthanum, less praseodymium and neodymium, and about the same amount of cerium as the Bayan Obo deposit.
The rare-earth content in selected minerals, including some bastnasites, is given in the table.
Rare-earth content in selected minerals (%)
rare-earth element bastnasite (Mountain Pass, California) bastnasite (Bayan Obo, China) monazite (Mount Weld, Australia) xenotime (Lehat, Malaysia) high-Y laterite (Longnan, China) low-Y laterite (Xunwu, China) loparite (Kola Peninsula, Russia)
La 33.8 23.0 25.5 1.2 1.8 43.4 25.0
Ce 49.6 50.0 46.7 3.1 0.4 2.4 50.5
Pr 4.1 6.2 5.3 0.5 0.7 9.0 5.0
Nd 11.2 18.5 18.5 1.6 3.0 31.7 15.0
Sm 0.9 0.8 2.3 1.1 2.8 3.9 0.7
Eu 0.1 0.2 0.4 trace 0.1 0.5 0.1
Gd 0.2 0.7 <0.1 3.5 6.9 3.0 0.6
Tb 0.0 0.1 <0.1 0.9 1.3 trace trace
Dy 0.0 0.1 0.1 8.3 6.7 trace 0.6
Ho 0.0 trace trace 2.0 1.6 trace 0.7
Er 0.0 trace trace 6.4 4.9 trace 0.8
Tm 0.0 trace none 1.1 0.7 trace 0.1
Yb 0.0 trace none 6.8 2.5 0.3 0.2
Lu trace trace none 1.0 0.4 0.1 0.2
Y 0.1 trace <0.1 61.0 65.0 8.0 1.3
Laterite clays
The laterite clays (also known as ion-absorption clays) are primarily composed of silica, alumina, and ferric oxide; those that also contain viable amounts of rare earths are found only in Jiangxi province of southeast China. Of the Jiangxi deposits, the clays located near Longnan are quite rich in the heavy lanthanides and yttrium. The clays at Xunwu have a most unusual distribution of rare earths, being rich in lanthanum and neodymium with a reasonably high yttrium content. The low concentrations of cerium and praseodymium in both clays, especially in the Xunwu clay, compared with the normal rare-earth distribution in the other minerals, is also remarkable. These clays are the main source of heavy elements used in rare-earth-containing products—e.g., dysprosium in Nd2Fe14B permanent magnets.
Monazite
Monazite, a phosphate, is the third most important ore source of rare earths. In the 1980s it accounted for 40 percent of the world’s production, but by 2010 it contributed only a small fraction to the mined rare earths. There were two reasons for this change: first, it is more costly to process monazite from the ore body to a rare-earth concentrate than to process bastnasite; second, monazite contains a significant amount of radioactive thorium dioxide (ThO2) compared with bastnasite, and thus special environmental procedures in handling and storage are needed. However, monazite is expected to contribute a growing share of mined rare earths as operations at Mount Weld, Australia, are brought up to full production by the end of 2014.
Monazite is widely distributed; in addition to Australia, it is found in India, Brazil, Malaysia, countries of the Commonwealth of Independent States, the United States, Thailand, Sri Lanka, the Democratic Republic of the Congo, South Korea, and South Africa.
Loparite
Loparite is a complex mineral that is mined primarily for its titanium, niobium, and tantalum content, with the rare earths extracted from the ore as a by-product. This ore is found mainly in the Kola Peninsula in northwest Russia and in Paraguay. Its rare-earth distribution is similar to that of bastnasite, except it has significantly higher concentrations of the heavy lanthanides and yttrium.
Xenotime
Xenotime is a phosphate mineral, similar to monazite except enriched in the heavy lanthanides and yttrium. It has been mined for many years but has contributed only about 1 percent of the total rare earths mined since the 1970s. Xenotime contains smaller amounts of the radioactive compounds U3O8 and ThO2 than monazite. Because of its high concentrations of yttrium and heavy lanthanides, xenotime is used as a source material for the individual rare-earth elements rather than being used as a mixture of heavy rare earths. The major producer of xenotime is Malaysia; deposits are also reported to exist in Norway and Brazil.
SpaceNext50
Electronic Structure And Ionic Radius
The chemical, metallurgical, and physical behaviours of the rare earths are governed by the electron configuration of these elements. In general, these elements are trivalent, R3+, but several of them have other valences. The number of 4f electrons of each lanthanide is given in the table of the number of 4f electrons and ionic radii for the R3+ ion. The 4f electrons have lower energies than and radially lie inside the outer three valence electrons (i.e., 4f electrons are “localized” and part of the ion core), and thus they do not directly participate in the bonding with other elements when a compound is formed. This is why the lanthanides are chemically similar and difficult to separate and why they occur together in various minerals. The outer or valence electrons for the 14 lanthanides and lanthanum are the same, 5d6s2; for scandium, 3d4s2; and for yttrium, 4d5s2. There is some variation in the chemical properties of the lanthanides because of the lanthanide contraction and the hybridization, or mixing, of the 4f electrons with the valence electrons.
electron probabilities for gadolinium
electron probabilities for gadolinium
Electron probabilities, P2(r), for the 4f, 5s, 5p, 5d, and 6s electrons of gadolinium.
Encyclopædia Britannica, Inc.
The systematic and smooth decrease from lanthanum to lutetium is known as the lanthanide contraction. It is due to the increase in the nuclear charge, which is not completely screened by the additional 4f electron as one goes from one lanthanide to the next. This increased effective charge draws the electrons (both the core and outer valence electrons) closer to the nucleus, thus accounting for the smaller radius of the higher-atomic-number lanthanides. The lanthanide contraction also accounts for the decreased basicity from lanthanum to lutetium and is the basis of various separation techniques.
As the 4f electrons are added when one moves across the lanthanide series from lanthanum to cerium to praseodymium and so on, the electrons, which have a magnetic moment due to the electron’s spin, maintain the same spin direction and the moments are aligned parallel with one another until the 4f level is half-filled—i.e., at seven 4f electrons in gadolinium. The next electron must align antiparallel in accordance with the Pauli exclusion principle, and thus two 4f electrons are paired. This continues until the 14th electron is added at lutetium, where all the 4f electron spins are paired up, and lutetium has no 4f magnetic moment.
The 4f electron configuration is extremely important and determines the magnetic and optical behaviours for the lanthanide elements; e.g., the peculiar properties of strong Nd2Fe14B permanent magnets are due to the three 4f electrons in neodymium, and the red colour in optical displays that use cathode-ray tubes is provided by the europium ion in a host compound, while the green colour is provided by terbium.
As noted above, several lanthanides may exhibit another valence state, R4+ for R = cerium, praseodymium, and terbium and R2+ for R = samarium, europium, and ytterbium. These additional valence states are a striking example of Hund’s rule, which states that empty, half-filled, and completely filled electronic levels tend to be more stable states: Ce4+ and Tb4+ give up an f electron to have an empty and half-filled 4f level, respectively, and Eu2+ and Yb2+ gain an f electron to have a half-filled or completely filled 4f level, respectively. Pr4+ and Sm2+ can, by giving up or gaining an f electron, respectively, in rare instances gain extra stability. In these two cases they tend toward but do not reach the respective empty or half-filled level. By giving up a 4f electron to become an R4+ ion, the radii of cerium, praseodymium, and terbium become smaller, 0.80, 0.78, and 0.76 Å, respectively. Conversely, samarium, europium, and ytterbium gain a 4f electron from the valence electrons to become an R2+ ion, and their radii increase to 1.19, 1.17, and 1.00 Å, respectively. Chemists have made use of these valence changes to separate Ce4+, Eu2+, and Yb2+ from the other trivalent R3 ions by relatively cheap chemical methods. CeO2 (where Ce is tetravalent) is the normal stable oxide form, while the oxides of praseodymium and terbium have the Pr6O11 and Tb4O7 stoichiometries containing both the tetra- and the trivalent states—i.e., 4PrO2∙Pr2O3 and 2TbO2∙Tb2O3, respectively. The divalent ions Sm2+, Eu2+, and Tb2+ form dihalides—e.g., SmCl2, EuCl2, and YbCl2. Several europium oxide stoichiometries are known: EuO (Eu2+), Eu2O3 (Eu3+), and Eu3O4 (i.e., EuO∙Eu2O3).
The ionic radius of scandium is much smaller than that of the smallest lanthanide, lutetium: 0.745 Å versus 0.861 Å. Scandium’s radius is slightly larger than those of the common metal ions—e.g., Fe3+, Nb5+, U5+, and W5+. This is the main reason why scandium is essentially absent from any of the normal rare-earth minerals, generally less than 0.01 percent by weight. However, scandium is obtained as a by-product of processing other ores (e.g, wolframite) and from mining tailings (e.g., uranium). On the other hand, the radius of yttrium, 0.9 Å, is nearly the same as that of holmium, 0.901 Å, and this accounts for the presence of yttrium in the heavy lanthanide minerals.
Most rare-earth metals have a valence of three; however, that of cerium is 3.2, and europium and ytterbium are divalent. This is quite evident when the metallic radii are plotted versus atomic number. The metallic radii of the trivalent metals exhibit the normal lanthanide contraction, but a noticeable deviation occurs for cerium, where its radius falls below the line established by the trivalent metals, and also for europium and ytterbium, where their radii lie well above this line.
metallic radii
metallic radii
Metallic radii of the rare-earth metals for a coordination number of 12 versus atomic number.
Encyclopædia Britannica, Inc.
The melting points for europium and ytterbium are significantly lower than those of the neighbouring trivalent lanthanides when they are plotted versus atomic number, and this is also consistent with the divalent nature of these two metals. Anomalies are also evident in other physical properties of europium and ytterbium compared with the trivalent lanthanide metals (see below Properties of the metals).
melting points and transformation temperatures
melting points and transformation temperatures
Melting points and transformation temperatures of rare-earth metals versus atomic number.
Encyclopædia Britannica, Inc.
The table presents the number of 4f electrons and the radius of the R3+ ion for the rare-earth elements.
Number of 4f electrons and
ionic radii for the R3+ ion
rare-earth
element number of
4f electrons number of
unpaired
4f electrons ionic
radius
(Å)
La 0 0 1.045
Ce 1 1 1.01
Pr 2 2 0.997
Nd 3 3 0.983
Pm 4 4 0.97
Sm 5 5 0.958
Eu 6 6 0.947
Gd 7 7 0.938
Tb 8 6 0.923
Dy 9 5 0.912
Ho 10 4 0.901
Er 11 3 0.890
Tm 12 2 0.880
Yb 13 1 0.868
Lu 14 0 0.861
Sc 0 0 0.745
Y 0 0 0.900
SpaceNext50
Processing Ores
All rare-earth ores contain less than 10 percent REO and must be upgraded to about 60 percent in order to be processed further. They are first ground to a powder and then separated from the other materials in the ore body by various standard processes that include magnetic and/or electrostatic separation and flotation. In the case of Mountain Pass bastnasite, a hot froth flotation process is used to remove the heavier products, barite (BaSO4) and celestite (SrSO4), by letting them settle out while the bastnasite and other light minerals are floated off. The 60 percent REO concentrate is treated with 10 percent HCl to dissolve the calcite (CaCO3). The insoluble residue, now 70 percent REO, is roasted to oxidize the Ce3+ to the Ce4+ state. After cooling, the material is leached with HCl dissolving the trivalent rare earths (lanthanum, praseodymium, neodymium, samarium, europium, and gadolinium), leaving behind the cerium concentrate, which is refined to various grades and marketed. The europium can be easily separated from the other lanthanides by reducing europium to divalent form, and the remaining dissolved lanthanides are separated by solvent extraction (see below Separation chemistry). The other bastnasite ores are treated in a similar manner, but the exact reagents and processes used vary with the other constituents found in the various ore bodies.
Monazite and xenotime ores are treated essentially the same way, since both are phosphate minerals. The monazite or xenotime is separated from the other minerals by a combination of gravity, electromagnetic, and electrostatic techniques, and then is cracked by either the acid process or the basic process. In the acid process the monazite or xenotime is treated with concentrated sulfuric acid at temperatures between 150 and 200 °C (302 and 392 °F). The solution contains soluble rare-earth and thorium sulfates and phosphates. The separation of thorium from the rare earths is quite complicated because the solubilities of both the thorium and the rare earths vary with temperature and acidity. At very low and intermediate acidities no separation is possible. At low acidity the thorium phosphate precipitates out of solution, and rare-earth sulfates remain in solution, while at high acidity the reverse occurs—the rare-earth sulfate is insoluble, and thorium is soluble. After the thorium has been removed from the rare earths, the latter are used as a mixed concentrate or are further processed for the individual elements (see below).
In the basic process, finely ground monazite or xenotime is mixed with a 70 percent sodium hydroxide (NaOH) solution and held in an autoclave at 140–150 °C (284–302 °F) for several hours. After the addition of water, the soluble sodium phosphate (Na3PO4) is recovered as a by-product from the insoluble R(OH)3, which still contains 5–10 percent thorium. Two different methods may be used to remove the thorium. In one method the hydroxide is dissolved in hydrogen chloride (HCl) or nitric acid (HNO3), and then the thorium hydroxide (Th(OH)4) is selectively precipitated by the addition of NaOH and/or ammonium hydroxide (NH4OH). In the other method HCl is added to the hydroxide to lower the pH to about 3 to dissolve the RCl3, and the insoluble Th(OH)4 is filtered off. The thorium-free rare-earth solution is converted to the hydrated chloride, carbonate, or hydroxide and sold as a mixed concentrate, or it can be used as the starting material for separating the individual elements (see below).
Separation Chemistry
The rare-earth separation processes in use today were developed during and shortly after World War II at several U.S. Atomic Energy Commission (AEC) laboratories. Work on the ion-exchange process was carried out at the Oak Ridge National Laboratory (Oak Ridge, Tennessee) by Gerald E. Boyd and coworkers and at the Ames Laboratory (Ames, Iowa) by Frank Harold Spedding and coworkers. Both groups showed that the ion-exchange process would work at least on a small scale for separating rare earths. In the 1950s the Ames group showed that it was possible to separate kilograms of high-purity (>99.99 percent) individual rare-earth elements. This was the beginning of the modern rare-earth industry in which large quantities of high-purity rare-earth elements became available for electronic, magnetic, phosphor, and optical applications.
Donald F. Peppard and colleagues at the Argonne National Laboratory (near Chicago, Illinois) and Boyd Weaver and coworkers at Oak Ridge National Laboratory developed the liquid-liquid solvent extraction method for separating rare earths in the mid-1950s. This method is used by all rare-earth producers to separate mixtures into the individual elements with purities ranging from 95 to 99.9 percent. The ion-exchange process is much slower, but higher purities of more than 99.99999 percent (i.e., 5 nines or better) can be attained. For optical and phosphor-grade materials, where purities of 5 to 6 nines are required, the individual rare-earth element is initially purified by solvent extraction up to about 99.9 percent purity, and then it is further processed by ion exchange to reach the purity required for the given application.
Ion exchange
In the ion-exchange process, a metal ion, R3+, in solution exchanges with three protons on a solid ion exchanger—a natural zeolite or a synthetic resin—that is normally called the resin. The tenacity with which the cation is held by the resin depends upon the size of the ion and its charge. However, no separation of the rare earths is possible, because the resin is not selective enough. By introducing a complexing agent, separation is possible; if the strength of the R3+ ion-complex of neighbouring lanthanide ions varies sufficiently from one rare earth to another, the separation will occur. Two common complexing agents used for separating the rare earths are ethylene diamine tetraacetate (EDTA) and hydroxyethylene diamine triacetate (HEDTA).
The resin spheres, about 0.1 mm (0.004 inch) diameter, are packed into a long column, and the resin bed is prepared by passing an acid through the column. Then it is loaded up with a mixed rare-earth acid solution that contains the complexing agent and a retaining ion, such as Cu2+ or Zn2+. The retaining ion is needed to prevent the first rare-earth ion from spreading out and being lost during the separation process. An eluant, ammonium (NH4), pushes the rare earths through the ion-exchange columns. The most stable complex comes out first—i.e., the copper or zinc complex, followed by lutetium, ytterbium, the other lanthanides (and yttrium, which usually comes out in the vicinity of dysprosium and holmium, depending upon the complexing agent), and finally lanthanum. The individual rare-earth R3+ complexes form rectangular bands with a minimum overlap of adjacent bands. The given rare-earth solution is collected, and the R3+ ion is precipitated out of solution using oxalic acid. The rare-earth oxalate is converted to the oxide by heating it in air at 800–1,000 °C (1,472–1,832 °F).
Solvent extraction
The liquid-liquid solvent extraction process uses two immiscible or partially immiscible solvents containing dissolved rare earths. The two liquids are mixed, the solutes are allowed to distribute between the two phases until equilibrium is established, and then the two liquids are separated. The concentrations of the solutes in the two phases depend upon the relative affinities for the two solvents. According to convention, the product (liquid) that contains the desired solute is called the “extract,” while the residue left behind in the other phase is called the “raffinate.” The best way to affect the separation of the rare earths is to use a multistage counter-current extractor on a continuous flow basis using many mixer-settler tanks or cells. For the case in which A has greater affinity for the organic phase and B has greater affinity for the aqueous phase, the organic phase becomes enriched in A and the aqueous phase enriched in B. It is much more complex for the rare-earth elements because there are several rare earths that are being separated simultaneously, not two as in the above example. Tributylphosphate (TBP) is used as the organic phase to extract the rare-earth ion from the highly acidic nitric acid aqueous phase. Other extractants, such as di-2-ethylhexyl orthophosphoric acid and long-chained amines, have also been used.
SpaceNext50
Preparation Of The Metals
There are several different processes of preparing the individual rare-earth metals, depending upon the given metal’s melting and boiling points (see below Properties of the metals) and the required purity of the metal for a given application. For high-purity metals (99 percent or better), the calciothermic and electrolytic processes are used for the low-melting lanthanides (lanthanum, cerium, praseodymium, and neodymium), the calciothermic process for the high-melting metals (scandium, yttrium, gadolinium, terbium, dysprosium, holmium, erbium, and lutetium, and another process (the so-called lanthanothermic process) for high-vapour-pressure metals (samarium, europium, thulium, and ytterbium). All three methods are used to prepare commercial-grade metals (95–98 percent pure).
Calciothermic method
The calciothermic process is used for all the rare-earth metals except the four with high vapour pressures—i.e., low boiling points. The rare-earth oxide is converted to the fluoride by heating it with anhydrous hydrogen fluoride (HF) gas to form RF3. The fluoride can also be made by first dissolving the oxide in aqueous HCl acid and then adding aqueous HF acid to precipitate the RF3 compound from the solution. The fluoride powder is mixed with calcium metal, placed in a tantalum crucible, and heated to 1,450 °C (2,642 °F) or higher, depending upon the melting point of R. The calcium reacts with the RF3 to form calcium fluoride (CaF2) and R. Because those two products do not mix with one another, the CaF2 floats on top of the metal. When cooled to room temperature, the CaF2 is readily separated from R. The metal is then heated in a high vacuum in a tantalum crucible to above its melting point to evaporate the excess calcium. At that point R may be further purified by sublimation or distillation. This procedure is used to prepare all the rare earths except samarium, europium, thulium, and ytterbium.
In China, calciothermic reduction on a commercial scale is commonly performed in graphite crucibles. This leads to a severe contamination of the produced metals with carbon, which readily dissolves in the molten rare-earth metals. Common oxide crucibles, such as aluminum oxide (Al2O3) or zirconia (ZrO2), are unsuitable for calciothermic reduction of the rare-earth metals because molten rare earths quickly reduce aluminum or zirconium, respectively, from their oxides, forming the corresponding rare-earth oxide.
Electrolytic method
The low-melting metals (lanthanum, cerium, praseodymium, and neodymium) may be prepared from the oxide by one of two electrolytic methods. The first method is to convert the oxide to the chloride (or fluoride) and then reduce the halide in an electrolytic cell. An electric current at a current density of about 10 A/cm2 is passed through the cell to reduce the RCl3 (RF3) to Cl2 (F2) gas at the carbon anode and liquid R metal at the molybdenum or tungsten cathode. The electrolyte is a molten salt composed of RCl3 (RF3) and NaCl (NaF). The lanthanides prepared electrolytically are not as pure as those made by the calciothermic process.
The second electrolytic process reduces the oxide directly in an RF3-LiF-CaF2 molten salt. The main problem with this process is that the oxide solubility is quite low, and it is difficult to control the oxygen solubility in the liquid salt solution.
The electrolytic process is limited to the rare-earth metals that melt below 1,050 °C (1,922 °F), because those that melt much higher react with the electrolytic cell and electrodes. As a result, the electrolytic cell and electrodes must be replaced quite often, and the produced rare-earth metals are highly contaminated.
Large commercial applications use the individual metals lanthanum for nickel–metal hydride batteries, neodymium for Nd2Fe14B permanent magnets, and misch metal for alloying agents and lighter flints. Misch metal is a mixture of the rare-earth elements that has been reduced from a rare-earth concentrate in which the rare-earth content is the same as in the mined ores (i.e., generally about 50 percent cerium, 25 percent lanthanum, 18 percent neodymium, and 7 percent praseodymium). The lanthanum and neodymium metals are prepared for the most part by the direct electrolytic reduction of the oxides. Misch metal is generally prepared by the electrolysis of the mixed RCl3.
Preparation of samarium, europium, thulium, and ytterbium: lanthanothermic process
The divalent metals europium and ytterbium have high vapour pressures—or lower boiling points than the other rare-earth elements, as can be seen when they are plotted versus atomic number—which makes it difficult to prepare them by the metallothermic or electrolytic methods. Samarium and thulium also have low boiling points, compared with the other lanthanide metals and also scandium and yttrium. The four metals with high vapour pressures are prepared by mixing R2O3 (R = samarium, europium, thulium, and ytterbium) with fine chips of lanthanum metal and placing the mixture in the bottom of a tall tantalum crucible. The mixture is heated to 1,400–1,600 °C (2,552–2,912 °F), depending on R. The lanthanum metal reacts with R2O3 to form lanthanum oxide (La2O3), and R evaporates and collects on a condenser at the top of the crucible that is about 500 °C (900 °F) colder than the reaction mixture at the bottom of the crucible. The four metals can be further purified by resubliming the metal.
boiling points
boiling points
Boiling points of rare-earth metals versus atomic number.
Encyclopædia Britannica, Inc.
SpaceNext50
WRITTEN BY: Karl A. Gschneidner, Jr.Vitalij K. Pecharsky
See Article History
Alternative Titles: inner transition element, rare-earth metal
Rare-earth element, any member of the group of chemical elements consisting of three elements in Group 3 (scandium [Sc], yttrium [Y], and lanthanum [La]) and the first extended row of elements below the main body of the periodic table (cerium [Ce] through lutetium [Lu]). The elements cerium through lutetium are called the lanthanides, but many scientists also, though incorrectly, call those elements rare earths.
The rare earths are generally trivalent elements, but a few have other valences. Cerium, praseodymium, and terbium can be tetravalent; samarium, europium and ytterbium, on the other hand, can be divalent. Many introductory science books view the rare earths as being so chemically similar to one another that collectively they can be considered as one element. To a certain degree that is correct—about 25 percent of their uses are based on this close similarity—but the other 75 percent of rare-earth usage is based on the unique properties of the individual elements. Furthermore, a close examination of these elements reveals vast differences in their behaviours and properties; e.g., the melting point of lanthanum, the prototype element of the lanthanide series (918 °C, or 1,684 °F), is much lower than the melting point of lutetium, the last element in the series (1,663 °C, or 3,025 °F). This difference is much larger than that found in many groups of the periodic table; e.g., the melting points of copper, silver, and gold vary by only about 100 °C (180 °F).
The name rare earths itself is a misnomer. At the time of their discovery in the 18th century, they were found to be a component of complex oxides, which were called “earths” at that time. Furthermore, these minerals seemed to be scarce, and thus these newly discovered elements were named “rare earths.” Actually, these elements are quite abundant and exist in many workable deposits throughout the world. The 16 naturally occurring rare earths fall into the 50th percentile of elemental abundances. By the early 21st century, China had become the world’s largest producer of rare-earth elements. Australia, Brazil, India, Kazakhstan, Malaysia, Russia, South Africa, and the United States also extract and refine significant quantities of these materials.
00:00
02:17
Many people do not realize the enormous impact the rare-earth elements have on their daily lives, but it is almost impossible to avoid a piece of modern technology that does not contain any. Even a product as simple as a lighter flint contains rare-earth elements. Their pervasiveness is exemplified by the modern automobile, one of the biggest consumers of rare-earth products. Dozens of electric motors in a typical automobile, as well as the speakers of its sound system, use neodymium-iron-boron permanent magnets. Electrical sensors employ yttria-stabilized zirconia to measure and control the oxygen content of the fuel. The three-way catalytic converter relies on cerium oxides to reduce nitrogen oxides to nitrogen gas and oxidize carbon monoxide to carbon dioxide and unburned hydrocarbons to carbon dioxide and water in the exhaust products. Phosphors in optical displays contain yttrium, europium, and terbium oxides. The windshield, mirrors, and lenses are polished using cerium oxides. Even the gasoline or diesel fuel that propels the vehicle was refined using rare-earth cracking catalysts containing lanthanum, cerium, or mixed-rare-earth oxides. Hybrid automobiles are powered by a nickel–lanthanum metal hydride rechargeable battery and an electrical traction motor, with permanent magnets containing rare-earth elements. In addition, modern media and communication devices—cell phones, televisions, and computers—all employ rare earths as magnets for speakers and hard drives and phosphors for optical displays. The amounts of rare earths used are quite small (0.1–5 percent by weight, except for permanent magnets, which contain about 25 percent neodymium), but they are critical, and any of those devices would not work as well, or would be significantly heavier, if it were not for the rare earths.
Get unlimited ad-free access to all Britannica’s trusted content.
Subscribe Today
Discovery And History
Although the rare earths have been around since the formation of Earth, their existence did not come to light until the late 18th century. In 1787 the Swedish army lieutenant Carl Axel Arrhenius discovered a unique black mineral in a small quarry in Ytterby (a small town near Stockholm). That mineral was a mixture of rare earths, and the first individual element to be isolated was cerium in 1803.
The history of the individual rare-earth elements is both complex and confused, mainly because of their chemical similarity. Many “newly discovered elements” were not one element but mixtures of as many as six different rare-earth elements. Furthermore, there were claims of discovery of a large number of other “elements,” which were supposed to be members of the rare-earth series but were not.
The last naturally occurring rare-earth element (lutetium) was discovered in 1907, but research into the chemistry of these elements was difficult because no one knew how many true rare-earth elements existed. Fortunately, in 1913–14 the research of Danish physicist Niels Bohr and English physicist Henry Gwyn Jeffreys Moseley resolved this situation. Bohr’s theory of the hydrogen atom enabled theoreticians to show that only 14 lanthanides exist. Moseley’s experimental studies verified the existence of 13 of these elements and showed that the 14th lanthanide must be element 61 and lie between neodymium and samarium.
In the 1920s the search for element 61 was intense. In 1926 groups of scientists at the University of Florence, Italy, and at the University of Illinois claimed to have discovered element 61 and named the element florentium and illinium, respectively, but their claims could not be independently verified. The furor of these claims and counterclaims eventually died down by 1930. It was not until 1947, after the fission of uranium, that element 61 definitely was isolated and named promethium by scientists at the U.S. Atomic Energy Commission’s Oak Ridge National Laboratory in Tennessee. (More details about the discovery of the individual elements are found in the articles about those elements.)
During the 160 years of discovery (1787–1947), the separation and purification of the rare-earth elements was a difficult and time-consuming process. Many scientists spent their whole lives attempting to obtain a 99 percent pure rare earth, usually by fractional crystallization, which makes use of the slight differences of the solubility of a rare-earth salt in an aqueous solution compared with that of a neighbouring lanthanide element.
Because the rare-earth elements were found to be fission products of the splitting of a uranium atom, the U.S. Atomic Energy Commission made a great effort to develop new methods for separating the rare-earth elements. However, in 1947 Gerald E. Boyd and colleagues at Oak Ridge National Laboratory and Frank Harold Spedding and colleagues at the Ames Laboratory in Iowa simultaneously published results which showed that ion-exchange processes offered a much better way for separating the rare earths.
SpaceNext50
Rare-earth element
KEY PEOPLE
Frank Harold Spedding
Carl Gustaf Mosander
RELATED TOPICS
Chemical element
Transition metal
Actinoid element
Gadolinium
Cerium
Lanthanum
Samarium
Neodymium
Ytterbium
Scandium
Abundance, Occurrence, And Reserves
As noted above, the rare earths are fairly abundant, but their availability is somewhat limited, primarily because their concentration levels in many ores are quite low (less than 5 percent by weight). An economically viable source should contain more than 5 percent rare earths, unless they are mined with another product—e.g., zirconium, uranium, or iron—which allows economic recovery of ore bodies with concentrations of as little as 0.5 percent by weight.
Of the 83 naturally occurring elements, the 16 naturally occurring rare-earth elements fall into the 50th percentile of the elemental abundances. Promethium, which is radioactive, with the most stable isotope having a half-life of 17.7 years, is not considered to be naturally occurring, although trace amounts have been found in some radioactive ores. Cerium, which is the most abundant, ranks 28th, and thulium, the least abundant, ranks 63rd. Collectively, the rare earths rank as the 22nd most abundant “element” (at the 68th percentile mark). The non-lanthanide rare-earth elements, yttrium and scandium, are 29th and 44th, respectively, in their abundances.
Lanthanum and the light lanthanides (cerium through europium) are more abundant than the heavy lanthanides (gadolinium through lutetium). Thus, the individual light lanthanide elements are generally less expensive than the heavy lanthanide elements. Furthermore, the metals with even atomic numbers (cerium, neodymium, samarium, gadolinium, dysprosium, erbium, and ytterbium) are more abundant than their neighbours with odd atomic numbers (lanthanum, praseodymium, promethium, europium, terbium, holmium, thulium, and lutetium).
Rare-earth ore deposits are found all over the world. The major ores are in China, the United States, Australia, and Russia, while other viable ore bodies are found in Canada, India, South Africa, and southeast Asia. The major minerals contained in these ore bodies are bastnasite (fluorocarbonate), monazite (phosphate), loparite [(R,Na,Sr,Ca)(Ti,Nb,Ta,Fe3+)O3], and laterite clays (SiO2, Al2O3, and Fe2O3).
Chinese deposits accounted for about 80 percent of the rare earths mined in the world in 2017 (105,000 tons of rare-earth oxide). About 94 percent of the rare earths mined in China are from bastnasite deposits. The major deposit is located at Bayan Obo, Inner Mongolia (83 percent), while smaller deposits are mined in Shandong (8 percent) and Sichuan (3 percent) provinces. About 3 percent comes from laterite (ion absorption) clays located in Jiangxi and Guangdong provinces in southern China, while the remaining 3 percent is produced at a variety of locations.
Officially, 130,000 metric tons of REO equivalent was mined in 2017, but a black market in rare earths was said to produce an additional 25 percent of that amount. Most black-market rare-earth materials are smuggled out of China.
China’s monopoly allowed it to raise prices by hundreds of percent for various rare-earth materials from 2009 to 2011 and also to impose export quotas on many of these products. This brought about a large change in the dynamics of the rare-earth markets. Mining of bastnasite resumed at Mountain Pass, California, in 2011 after a nine-year hiatus, and mining of monazite began that same year at Mount Weld, Australia. At the same time, loparite was being mined in Russia, while monazite was mined in India, Vietnam, Thailand, and Malaysia. Those and other mining operations brought a new equilibrium between demand and supply in which China was still the major supplier of rare-earth minerals, but companies either sought alternative sources, used less, or recycled more rare earths.
As of 2017, known world reserves of rare-earth minerals amounted to some 120 million metric tons of contained REO. China has the largest fraction (37 percent), followed by Brazil and Vietnam (18 percent each), Russia (15 percent), and the remaining countries (12 percent). With reserves this large, the world would not run out of rare earths for more than 900 years if demand for the minerals would remain at 2017 levels. Historically, however, demand for rare earths has risen at a rate of about 10 percent per year. If demand continued to grow at this rate and no recycling of produced rare earths were undertaken, known world reserves likely would be exhausted sometime after the mid-21st century.
Considering both the limited reserves and high value of the rare-earth metals, recycling these elements from consumer products that reach the end of their useful life is expected to become more important. At present, only scrap metal, magnet materials, and compounds used in the manufacture of phosphors and catalysts are recycled. However, products that contain relatively large amounts of rare earths could be recycled immediately using existing techniques. These include rechargeable nickel–metal hydride batteries that contain a few grams to a few kilograms of LaNi5-based alloys as a hydrogen absorber as well as large SmCo5- and Nd2Fe14B-based permanent magnets. All of these materials hold 25–30 percent by weight light lanthanides—much more than even the best rare-earth-containing ore (see below). However, the majority of consumer electronic devices contain only small amounts of rare earths. For example, a hard drive’s spindle magnet contains only a few grams of Nd2Fe14B. A speaker magnet of a cellular phone makes up less than 0.1 percent of the total mass of the telephone. A compact fluorescent lamp has only a fraction of a gram of lanthanide metals in the phosphor. Considering the complexity of many modern electronic devices, recycling of rare earths must be done simultaneously with recycling of other valuable resources and potentially dangerous substances. These include precious metals (such as silver, gold, and palladium), nonferrous metals (such as aluminum, cobalt, nickel, copper, gallium, and zinc), carcinogens (such as cadmium), poisons (such as mercury, lead, and beryllium), plastics, glass, and ceramics. Numerous scientific and engineering issues, therefore, must be resolved, first, in order to create consumer products that are easily recyclable at the end of their life and, second, to make recycling of rare earths both meaningful and economical, thus making the best use of the rare earths—an extremely valuable but limited resource provided by nature.
SpaceNext50
SIMILAR TOPICS
Hydrogen
Alkali metal
Alkaline-earth metal
Carbon group element
Boron group element
Oxygen group element
Nitrogen group element
Halogen
Noble gas
Zinc group element
Minerals And Ores
The content of the individual rare-earth elements varies considerably from mineral to mineral and from deposit to deposit. The minerals and ores are generally classified as “light” or “heavy”; in the former group most of the elements present are the light-atomic-weight elements (i.e., lanthanum, cerium, praseodymium, neodymium, samarium, and europium), whereas most of the elements in the latter group are the heavy-atomic-weight elements (i.e., gadolinium, terbium, dysprosium, holmium, erbium, thulium, ytterbium, and lutetium, plus yttrium, which is considered to be a member of the heavy group because it is found in the ores with the heavy lanthanides). The geochemistry of scandium is significantly different from the geochemistry of the other rare-earth elements. Information on its ores and minerals is provided in the article scandium. Essentially no scandium is found in any of the minerals discussed below.
Of the approximately 160 minerals that are known to contain rare earths, only four are currently mined for their rare earths: bastnasite, laterite clays, monazite, and loparite. With the exception of laterite clays, these minerals are good sources of light lanthanides and lanthanum and account for about 95 percent of the rare earths in use. Laterite clays are a commercial source of the heavy lanthanides and yttrium.
Other minerals that have been used as a source of rare earths are apatite, euxenite, gadolinite, and xenotime. Allanite, fluorite, perovskite, sphene, and zircon have the potential to be future sources of rare earths. (In addition, uranium and iron tailings have been used in the past as a source of the heavy lanthanides plus yttrium and of the light lanthanides plus lanthanum, respectively.) Many of these minerals such as apatite and euxenite are processed for other constituents, and the rare earths could be extracted as a by-product. In addition to minerals found in Earth’s crust, there are some deep-sea muds, such as those near Minamitori Island, Japan, that contain rare-earth elements. The concentrations vary from hundreds to thousands of parts per million, and these muds may one day be a source of rare earths.
The idealized chemical compositions of these 13 minerals that are sources of rare earths are given in the table.
Composition of selected rare-earth minerals
name idealized composition primary rare-earth content
allanite (Ca,Fe2+)(R,Al,Fe3+)3Si3O13H R = light lanthanoids
apatite Ca5(PO4)3F R = light lanthanoids
bastnasite RCO3F R = light lanthanoids (60–70%)
euxenite R(Nb,Ta)TiO6 ∙ xH2O R = heavy lanthanoids plus Y (15–43%)
fluorite CaF2 R = heavy lanthanoids plus Y
gadolinite R2(Fe2+,Be)3Si2O10 R = heavy lanthanoids plus Y (34–65%)
laterite clays SiO2, Al2O3, Fe2O3 R = heavy lanthanoids plus Y
loparite (R,Na,Sr,Ca)(Ti,Nb,Ta,Fe3+)O3 R = light lanthanoids (32–34%)
monazite RPO4 R = light lanthanoids (50–78%)
perovskite CaTiO3 R = light lanthanoids
sphene CaTiSiO4X2 (X = ½O2−, OH−, or F−) R = light lanthanoids
xenotime RPO4 R = heavy lanthanoids plus Y (54–65%)
zircon ZrSiO2 R = both light and heavy lanthanoids plus Y
Bastnasite
Bastnasite, a fluorocarbonate, is the principal source of rare earths. About 94 percent of the rare earths used in the world come from mines in Mountain Pass, California, U.S.; Bayan Obo, Inner Mongolia, China; Shandong province, China; and Sichuan province, China. The Bayan Obo deposit is slightly richer in praseodymium and neodymium than the Mountain Pass bastnasite is, primarily at the expense of the lanthanum content, which is 10 percent greater in the Mountain Pass ore. The rare-earth contents of the Shandong and Sichuan minerals are slightly different from that of the Bayan Obo minerals and also from each other’s. The Shandong bastnasite is similar to the Mountain Pass mineral. The Sichuan ore has more lanthanum, less praseodymium and neodymium, and about the same amount of cerium as the Bayan Obo deposit.
The rare-earth content in selected minerals, including some bastnasites, is given in the table.
Rare-earth content in selected minerals (%)
rare-earth element bastnasite (Mountain Pass, California) bastnasite (Bayan Obo, China) monazite (Mount Weld, Australia) xenotime (Lehat, Malaysia) high-Y laterite (Longnan, China) low-Y laterite (Xunwu, China) loparite (Kola Peninsula, Russia)
La 33.8 23.0 25.5 1.2 1.8 43.4 25.0
Ce 49.6 50.0 46.7 3.1 0.4 2.4 50.5
Pr 4.1 6.2 5.3 0.5 0.7 9.0 5.0
Nd 11.2 18.5 18.5 1.6 3.0 31.7 15.0
Sm 0.9 0.8 2.3 1.1 2.8 3.9 0.7
Eu 0.1 0.2 0.4 trace 0.1 0.5 0.1
Gd 0.2 0.7 <0.1 3.5 6.9 3.0 0.6
Tb 0.0 0.1 <0.1 0.9 1.3 trace trace
Dy 0.0 0.1 0.1 8.3 6.7 trace 0.6
Ho 0.0 trace trace 2.0 1.6 trace 0.7
Er 0.0 trace trace 6.4 4.9 trace 0.8
Tm 0.0 trace none 1.1 0.7 trace 0.1
Yb 0.0 trace none 6.8 2.5 0.3 0.2
Lu trace trace none 1.0 0.4 0.1 0.2
Y 0.1 trace <0.1 61.0 65.0 8.0 1.3
Laterite clays
The laterite clays (also known as ion-absorption clays) are primarily composed of silica, alumina, and ferric oxide; those that also contain viable amounts of rare earths are found only in Jiangxi province of southeast China. Of the Jiangxi deposits, the clays located near Longnan are quite rich in the heavy lanthanides and yttrium. The clays at Xunwu have a most unusual distribution of rare earths, being rich in lanthanum and neodymium with a reasonably high yttrium content. The low concentrations of cerium and praseodymium in both clays, especially in the Xunwu clay, compared with the normal rare-earth distribution in the other minerals, is also remarkable. These clays are the main source of heavy elements used in rare-earth-containing products—e.g., dysprosium in Nd2Fe14B permanent magnets.
Monazite
Monazite, a phosphate, is the third most important ore source of rare earths. In the 1980s it accounted for 40 percent of the world’s production, but by 2010 it contributed only a small fraction to the mined rare earths. There were two reasons for this change: first, it is more costly to process monazite from the ore body to a rare-earth concentrate than to process bastnasite; second, monazite contains a significant amount of radioactive thorium dioxide (ThO2) compared with bastnasite, and thus special environmental procedures in handling and storage are needed. However, monazite is expected to contribute a growing share of mined rare earths as operations at Mount Weld, Australia, are brought up to full production by the end of 2014.
Monazite is widely distributed; in addition to Australia, it is found in India, Brazil, Malaysia, countries of the Commonwealth of Independent States, the United States, Thailand, Sri Lanka, the Democratic Republic of the Congo, South Korea, and South Africa.
Loparite
Loparite is a complex mineral that is mined primarily for its titanium, niobium, and tantalum content, with the rare earths extracted from the ore as a by-product. This ore is found mainly in the Kola Peninsula in northwest Russia and in Paraguay. Its rare-earth distribution is similar to that of bastnasite, except it has significantly higher concentrations of the heavy lanthanides and yttrium.
Xenotime
Xenotime is a phosphate mineral, similar to monazite except enriched in the heavy lanthanides and yttrium. It has been mined for many years but has contributed only about 1 percent of the total rare earths mined since the 1970s. Xenotime contains smaller amounts of the radioactive compounds U3O8 and ThO2 than monazite. Because of its high concentrations of yttrium and heavy lanthanides, xenotime is used as a source material for the individual rare-earth elements rather than being used as a mixture of heavy rare earths. The major producer of xenotime is Malaysia; deposits are also reported to exist in Norway and Brazil.
SpaceNext50
Electronic Structure And Ionic Radius
The chemical, metallurgical, and physical behaviours of the rare earths are governed by the electron configuration of these elements. In general, these elements are trivalent, R3+, but several of them have other valences. The number of 4f electrons of each lanthanide is given in the table of the number of 4f electrons and ionic radii for the R3+ ion. The 4f electrons have lower energies than and radially lie inside the outer three valence electrons (i.e., 4f electrons are “localized” and part of the ion core), and thus they do not directly participate in the bonding with other elements when a compound is formed. This is why the lanthanides are chemically similar and difficult to separate and why they occur together in various minerals. The outer or valence electrons for the 14 lanthanides and lanthanum are the same, 5d6s2; for scandium, 3d4s2; and for yttrium, 4d5s2. There is some variation in the chemical properties of the lanthanides because of the lanthanide contraction and the hybridization, or mixing, of the 4f electrons with the valence electrons.
electron probabilities for gadolinium
electron probabilities for gadolinium
Electron probabilities, P2(r), for the 4f, 5s, 5p, 5d, and 6s electrons of gadolinium.
Encyclopædia Britannica, Inc.
The systematic and smooth decrease from lanthanum to lutetium is known as the lanthanide contraction. It is due to the increase in the nuclear charge, which is not completely screened by the additional 4f electron as one goes from one lanthanide to the next. This increased effective charge draws the electrons (both the core and outer valence electrons) closer to the nucleus, thus accounting for the smaller radius of the higher-atomic-number lanthanides. The lanthanide contraction also accounts for the decreased basicity from lanthanum to lutetium and is the basis of various separation techniques.
As the 4f electrons are added when one moves across the lanthanide series from lanthanum to cerium to praseodymium and so on, the electrons, which have a magnetic moment due to the electron’s spin, maintain the same spin direction and the moments are aligned parallel with one another until the 4f level is half-filled—i.e., at seven 4f electrons in gadolinium. The next electron must align antiparallel in accordance with the Pauli exclusion principle, and thus two 4f electrons are paired. This continues until the 14th electron is added at lutetium, where all the 4f electron spins are paired up, and lutetium has no 4f magnetic moment.
The 4f electron configuration is extremely important and determines the magnetic and optical behaviours for the lanthanide elements; e.g., the peculiar properties of strong Nd2Fe14B permanent magnets are due to the three 4f electrons in neodymium, and the red colour in optical displays that use cathode-ray tubes is provided by the europium ion in a host compound, while the green colour is provided by terbium.
As noted above, several lanthanides may exhibit another valence state, R4+ for R = cerium, praseodymium, and terbium and R2+ for R = samarium, europium, and ytterbium. These additional valence states are a striking example of Hund’s rule, which states that empty, half-filled, and completely filled electronic levels tend to be more stable states: Ce4+ and Tb4+ give up an f electron to have an empty and half-filled 4f level, respectively, and Eu2+ and Yb2+ gain an f electron to have a half-filled or completely filled 4f level, respectively. Pr4+ and Sm2+ can, by giving up or gaining an f electron, respectively, in rare instances gain extra stability. In these two cases they tend toward but do not reach the respective empty or half-filled level. By giving up a 4f electron to become an R4+ ion, the radii of cerium, praseodymium, and terbium become smaller, 0.80, 0.78, and 0.76 Å, respectively. Conversely, samarium, europium, and ytterbium gain a 4f electron from the valence electrons to become an R2+ ion, and their radii increase to 1.19, 1.17, and 1.00 Å, respectively. Chemists have made use of these valence changes to separate Ce4+, Eu2+, and Yb2+ from the other trivalent R3 ions by relatively cheap chemical methods. CeO2 (where Ce is tetravalent) is the normal stable oxide form, while the oxides of praseodymium and terbium have the Pr6O11 and Tb4O7 stoichiometries containing both the tetra- and the trivalent states—i.e., 4PrO2∙Pr2O3 and 2TbO2∙Tb2O3, respectively. The divalent ions Sm2+, Eu2+, and Tb2+ form dihalides—e.g., SmCl2, EuCl2, and YbCl2. Several europium oxide stoichiometries are known: EuO (Eu2+), Eu2O3 (Eu3+), and Eu3O4 (i.e., EuO∙Eu2O3).
The ionic radius of scandium is much smaller than that of the smallest lanthanide, lutetium: 0.745 Å versus 0.861 Å. Scandium’s radius is slightly larger than those of the common metal ions—e.g., Fe3+, Nb5+, U5+, and W5+. This is the main reason why scandium is essentially absent from any of the normal rare-earth minerals, generally less than 0.01 percent by weight. However, scandium is obtained as a by-product of processing other ores (e.g, wolframite) and from mining tailings (e.g., uranium). On the other hand, the radius of yttrium, 0.9 Å, is nearly the same as that of holmium, 0.901 Å, and this accounts for the presence of yttrium in the heavy lanthanide minerals.
Most rare-earth metals have a valence of three; however, that of cerium is 3.2, and europium and ytterbium are divalent. This is quite evident when the metallic radii are plotted versus atomic number. The metallic radii of the trivalent metals exhibit the normal lanthanide contraction, but a noticeable deviation occurs for cerium, where its radius falls below the line established by the trivalent metals, and also for europium and ytterbium, where their radii lie well above this line.
metallic radii
metallic radii
Metallic radii of the rare-earth metals for a coordination number of 12 versus atomic number.
Encyclopædia Britannica, Inc.
The melting points for europium and ytterbium are significantly lower than those of the neighbouring trivalent lanthanides when they are plotted versus atomic number, and this is also consistent with the divalent nature of these two metals. Anomalies are also evident in other physical properties of europium and ytterbium compared with the trivalent lanthanide metals (see below Properties of the metals).
melting points and transformation temperatures
melting points and transformation temperatures
Melting points and transformation temperatures of rare-earth metals versus atomic number.
Encyclopædia Britannica, Inc.
The table presents the number of 4f electrons and the radius of the R3+ ion for the rare-earth elements.
Number of 4f electrons and
ionic radii for the R3+ ion
rare-earth
element number of
4f electrons number of
unpaired
4f electrons ionic
radius
(Å)
La 0 0 1.045
Ce 1 1 1.01
Pr 2 2 0.997
Nd 3 3 0.983
Pm 4 4 0.97
Sm 5 5 0.958
Eu 6 6 0.947
Gd 7 7 0.938
Tb 8 6 0.923
Dy 9 5 0.912
Ho 10 4 0.901
Er 11 3 0.890
Tm 12 2 0.880
Yb 13 1 0.868
Lu 14 0 0.861
Sc 0 0 0.745
Y 0 0 0.900
SpaceNext50
Processing Ores
All rare-earth ores contain less than 10 percent REO and must be upgraded to about 60 percent in order to be processed further. They are first ground to a powder and then separated from the other materials in the ore body by various standard processes that include magnetic and/or electrostatic separation and flotation. In the case of Mountain Pass bastnasite, a hot froth flotation process is used to remove the heavier products, barite (BaSO4) and celestite (SrSO4), by letting them settle out while the bastnasite and other light minerals are floated off. The 60 percent REO concentrate is treated with 10 percent HCl to dissolve the calcite (CaCO3). The insoluble residue, now 70 percent REO, is roasted to oxidize the Ce3+ to the Ce4+ state. After cooling, the material is leached with HCl dissolving the trivalent rare earths (lanthanum, praseodymium, neodymium, samarium, europium, and gadolinium), leaving behind the cerium concentrate, which is refined to various grades and marketed. The europium can be easily separated from the other lanthanides by reducing europium to divalent form, and the remaining dissolved lanthanides are separated by solvent extraction (see below Separation chemistry). The other bastnasite ores are treated in a similar manner, but the exact reagents and processes used vary with the other constituents found in the various ore bodies.
Monazite and xenotime ores are treated essentially the same way, since both are phosphate minerals. The monazite or xenotime is separated from the other minerals by a combination of gravity, electromagnetic, and electrostatic techniques, and then is cracked by either the acid process or the basic process. In the acid process the monazite or xenotime is treated with concentrated sulfuric acid at temperatures between 150 and 200 °C (302 and 392 °F). The solution contains soluble rare-earth and thorium sulfates and phosphates. The separation of thorium from the rare earths is quite complicated because the solubilities of both the thorium and the rare earths vary with temperature and acidity. At very low and intermediate acidities no separation is possible. At low acidity the thorium phosphate precipitates out of solution, and rare-earth sulfates remain in solution, while at high acidity the reverse occurs—the rare-earth sulfate is insoluble, and thorium is soluble. After the thorium has been removed from the rare earths, the latter are used as a mixed concentrate or are further processed for the individual elements (see below).
In the basic process, finely ground monazite or xenotime is mixed with a 70 percent sodium hydroxide (NaOH) solution and held in an autoclave at 140–150 °C (284–302 °F) for several hours. After the addition of water, the soluble sodium phosphate (Na3PO4) is recovered as a by-product from the insoluble R(OH)3, which still contains 5–10 percent thorium. Two different methods may be used to remove the thorium. In one method the hydroxide is dissolved in hydrogen chloride (HCl) or nitric acid (HNO3), and then the thorium hydroxide (Th(OH)4) is selectively precipitated by the addition of NaOH and/or ammonium hydroxide (NH4OH). In the other method HCl is added to the hydroxide to lower the pH to about 3 to dissolve the RCl3, and the insoluble Th(OH)4 is filtered off. The thorium-free rare-earth solution is converted to the hydrated chloride, carbonate, or hydroxide and sold as a mixed concentrate, or it can be used as the starting material for separating the individual elements (see below).
Separation Chemistry
The rare-earth separation processes in use today were developed during and shortly after World War II at several U.S. Atomic Energy Commission (AEC) laboratories. Work on the ion-exchange process was carried out at the Oak Ridge National Laboratory (Oak Ridge, Tennessee) by Gerald E. Boyd and coworkers and at the Ames Laboratory (Ames, Iowa) by Frank Harold Spedding and coworkers. Both groups showed that the ion-exchange process would work at least on a small scale for separating rare earths. In the 1950s the Ames group showed that it was possible to separate kilograms of high-purity (>99.99 percent) individual rare-earth elements. This was the beginning of the modern rare-earth industry in which large quantities of high-purity rare-earth elements became available for electronic, magnetic, phosphor, and optical applications.
Donald F. Peppard and colleagues at the Argonne National Laboratory (near Chicago, Illinois) and Boyd Weaver and coworkers at Oak Ridge National Laboratory developed the liquid-liquid solvent extraction method for separating rare earths in the mid-1950s. This method is used by all rare-earth producers to separate mixtures into the individual elements with purities ranging from 95 to 99.9 percent. The ion-exchange process is much slower, but higher purities of more than 99.99999 percent (i.e., 5 nines or better) can be attained. For optical and phosphor-grade materials, where purities of 5 to 6 nines are required, the individual rare-earth element is initially purified by solvent extraction up to about 99.9 percent purity, and then it is further processed by ion exchange to reach the purity required for the given application.
Ion exchange
In the ion-exchange process, a metal ion, R3+, in solution exchanges with three protons on a solid ion exchanger—a natural zeolite or a synthetic resin—that is normally called the resin. The tenacity with which the cation is held by the resin depends upon the size of the ion and its charge. However, no separation of the rare earths is possible, because the resin is not selective enough. By introducing a complexing agent, separation is possible; if the strength of the R3+ ion-complex of neighbouring lanthanide ions varies sufficiently from one rare earth to another, the separation will occur. Two common complexing agents used for separating the rare earths are ethylene diamine tetraacetate (EDTA) and hydroxyethylene diamine triacetate (HEDTA).
The resin spheres, about 0.1 mm (0.004 inch) diameter, are packed into a long column, and the resin bed is prepared by passing an acid through the column. Then it is loaded up with a mixed rare-earth acid solution that contains the complexing agent and a retaining ion, such as Cu2+ or Zn2+. The retaining ion is needed to prevent the first rare-earth ion from spreading out and being lost during the separation process. An eluant, ammonium (NH4), pushes the rare earths through the ion-exchange columns. The most stable complex comes out first—i.e., the copper or zinc complex, followed by lutetium, ytterbium, the other lanthanides (and yttrium, which usually comes out in the vicinity of dysprosium and holmium, depending upon the complexing agent), and finally lanthanum. The individual rare-earth R3+ complexes form rectangular bands with a minimum overlap of adjacent bands. The given rare-earth solution is collected, and the R3+ ion is precipitated out of solution using oxalic acid. The rare-earth oxalate is converted to the oxide by heating it in air at 800–1,000 °C (1,472–1,832 °F).
Solvent extraction
The liquid-liquid solvent extraction process uses two immiscible or partially immiscible solvents containing dissolved rare earths. The two liquids are mixed, the solutes are allowed to distribute between the two phases until equilibrium is established, and then the two liquids are separated. The concentrations of the solutes in the two phases depend upon the relative affinities for the two solvents. According to convention, the product (liquid) that contains the desired solute is called the “extract,” while the residue left behind in the other phase is called the “raffinate.” The best way to affect the separation of the rare earths is to use a multistage counter-current extractor on a continuous flow basis using many mixer-settler tanks or cells. For the case in which A has greater affinity for the organic phase and B has greater affinity for the aqueous phase, the organic phase becomes enriched in A and the aqueous phase enriched in B. It is much more complex for the rare-earth elements because there are several rare earths that are being separated simultaneously, not two as in the above example. Tributylphosphate (TBP) is used as the organic phase to extract the rare-earth ion from the highly acidic nitric acid aqueous phase. Other extractants, such as di-2-ethylhexyl orthophosphoric acid and long-chained amines, have also been used.
SpaceNext50
Preparation Of The Metals
There are several different processes of preparing the individual rare-earth metals, depending upon the given metal’s melting and boiling points (see below Properties of the metals) and the required purity of the metal for a given application. For high-purity metals (99 percent or better), the calciothermic and electrolytic processes are used for the low-melting lanthanides (lanthanum, cerium, praseodymium, and neodymium), the calciothermic process for the high-melting metals (scandium, yttrium, gadolinium, terbium, dysprosium, holmium, erbium, and lutetium, and another process (the so-called lanthanothermic process) for high-vapour-pressure metals (samarium, europium, thulium, and ytterbium). All three methods are used to prepare commercial-grade metals (95–98 percent pure).
Calciothermic method
The calciothermic process is used for all the rare-earth metals except the four with high vapour pressures—i.e., low boiling points. The rare-earth oxide is converted to the fluoride by heating it with anhydrous hydrogen fluoride (HF) gas to form RF3. The fluoride can also be made by first dissolving the oxide in aqueous HCl acid and then adding aqueous HF acid to precipitate the RF3 compound from the solution. The fluoride powder is mixed with calcium metal, placed in a tantalum crucible, and heated to 1,450 °C (2,642 °F) or higher, depending upon the melting point of R. The calcium reacts with the RF3 to form calcium fluoride (CaF2) and R. Because those two products do not mix with one another, the CaF2 floats on top of the metal. When cooled to room temperature, the CaF2 is readily separated from R. The metal is then heated in a high vacuum in a tantalum crucible to above its melting point to evaporate the excess calcium. At that point R may be further purified by sublimation or distillation. This procedure is used to prepare all the rare earths except samarium, europium, thulium, and ytterbium.
In China, calciothermic reduction on a commercial scale is commonly performed in graphite crucibles. This leads to a severe contamination of the produced metals with carbon, which readily dissolves in the molten rare-earth metals. Common oxide crucibles, such as aluminum oxide (Al2O3) or zirconia (ZrO2), are unsuitable for calciothermic reduction of the rare-earth metals because molten rare earths quickly reduce aluminum or zirconium, respectively, from their oxides, forming the corresponding rare-earth oxide.
Electrolytic method
The low-melting metals (lanthanum, cerium, praseodymium, and neodymium) may be prepared from the oxide by one of two electrolytic methods. The first method is to convert the oxide to the chloride (or fluoride) and then reduce the halide in an electrolytic cell. An electric current at a current density of about 10 A/cm2 is passed through the cell to reduce the RCl3 (RF3) to Cl2 (F2) gas at the carbon anode and liquid R metal at the molybdenum or tungsten cathode. The electrolyte is a molten salt composed of RCl3 (RF3) and NaCl (NaF). The lanthanides prepared electrolytically are not as pure as those made by the calciothermic process.
The second electrolytic process reduces the oxide directly in an RF3-LiF-CaF2 molten salt. The main problem with this process is that the oxide solubility is quite low, and it is difficult to control the oxygen solubility in the liquid salt solution.
The electrolytic process is limited to the rare-earth metals that melt below 1,050 °C (1,922 °F), because those that melt much higher react with the electrolytic cell and electrodes. As a result, the electrolytic cell and electrodes must be replaced quite often, and the produced rare-earth metals are highly contaminated.
Large commercial applications use the individual metals lanthanum for nickel–metal hydride batteries, neodymium for Nd2Fe14B permanent magnets, and misch metal for alloying agents and lighter flints. Misch metal is a mixture of the rare-earth elements that has been reduced from a rare-earth concentrate in which the rare-earth content is the same as in the mined ores (i.e., generally about 50 percent cerium, 25 percent lanthanum, 18 percent neodymium, and 7 percent praseodymium). The lanthanum and neodymium metals are prepared for the most part by the direct electrolytic reduction of the oxides. Misch metal is generally prepared by the electrolysis of the mixed RCl3.
Preparation of samarium, europium, thulium, and ytterbium: lanthanothermic process
The divalent metals europium and ytterbium have high vapour pressures—or lower boiling points than the other rare-earth elements, as can be seen when they are plotted versus atomic number—which makes it difficult to prepare them by the metallothermic or electrolytic methods. Samarium and thulium also have low boiling points, compared with the other lanthanide metals and also scandium and yttrium. The four metals with high vapour pressures are prepared by mixing R2O3 (R = samarium, europium, thulium, and ytterbium) with fine chips of lanthanum metal and placing the mixture in the bottom of a tall tantalum crucible. The mixture is heated to 1,400–1,600 °C (2,552–2,912 °F), depending on R. The lanthanum metal reacts with R2O3 to form lanthanum oxide (La2O3), and R evaporates and collects on a condenser at the top of the crucible that is about 500 °C (900 °F) colder than the reaction mixture at the bottom of the crucible. The four metals can be further purified by resubliming the metal.
boiling points
boiling points
Boiling points of rare-earth metals versus atomic number.
Encyclopædia Britannica, Inc.
SpaceNext50
-
- Posts: 1355
- Joined: Wed Dec 28, 2016 10:56 am
Re: What happens if China restricts rare earths supply ?
Now the BigP Oracle is becoming ridiculous furiously parroting stuff he has not the remotest clue about.
Anyone can mindlessly copy tech stuff. But BigP is trying to protect his rapidly slipping Oracle status.
He has no understanding whatsoever about the practical commercial issues. The FAKE NEWS will come next.
But ignoring the struggling Oracle and back to the topic and something relevant and interesting.
The Geopolitics of Rare Earth Elements
Apr 8, 2019 | 09:00 GMT
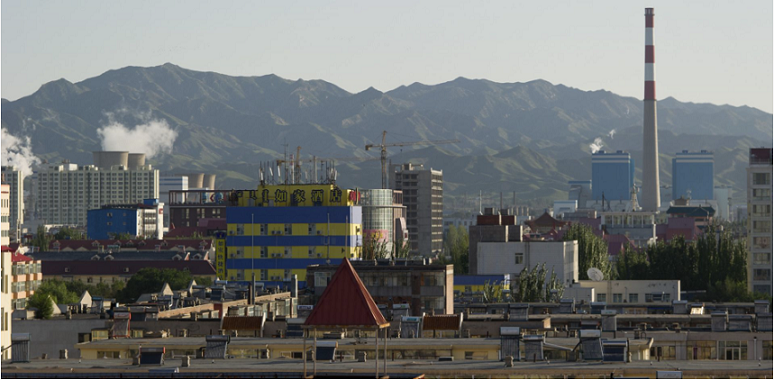
The skyline of the Inner Mongolian city of Baotou is blackened by pollution from factories processing rare earth elements, which are essential for the production of mobile phones and computers.
Pollution from factories processing rare earth elements, which are essential for the production of mobile phones and computers, blackens the skyline of Baotou, in Inner Mongolia. (Ed Jones/AFP/Getty Images)
HIGHLIGHTS
Demand for rare earth elements will grow in the next several years as the world undergoes an energy transition, but the supply chain is vulnerable.
China is the top supplier in the market, but its own growing domestic demand may lessen its dominance by driving increased production outside its own borders.
The U.S. defense industry makes up a small portion of the total demand for rare earth elements. To ensure supply alternatives from China, the U.S. government will likely need to proactively intervene in the market to shift production dependence away from China.
Editor's Note: At Stratfor, we use geopolitics to understand the constraints and advantages that geography confers on a country and the political, technological and economic decisions it compels. The exercise, taken to its logical conclusion, can extend all the way down to an atomic level. This occasional series examines the elements and the power that various combinations of protons, neutrons and electrons can exert on the world around us. In the latest installment, we look at rare earth elements.
Tucked into the sixth row of the periodic table, often represented by a single square expanded like a footnote at the bottom of the table, are the 15 lanthanides. When combined with yttrium and scandium, these materials are better known as the rare earth elements. Though they are used in very small amounts, their significance to the U.S. defense sector and to emerging and potentially disruptive technologies, combined with China's control over the majority of the market, has given the rare earth elements outsized geopolitical relevance.
The Big Picture
Each element on the periodic table tells a geopolitical story. The rare earth elements, individually and as a whole group, are the quintessential symbol for the emerging, shifting global order, as China and the United States engage in both a trade war that may soon be resolved and a tech war that will continue for decades.
The rare earth elements are already critical to the U.S. defense sector, but rare earth mining, processing and fabrication capabilities will even more strongly influence geopolitical dynamics in the coming years as the world undergoes its nascent energy transition and transportation evolution. In the near term, China will benefit from its near-monopoly, but ultimately its own growing domestic demand will limit the duration of its control over the sector and eventually force production diversification.
The Same but Different
Though they are often discussed as a group, rare earth elements have individual qualities that funnel them into specific use cases and markets. From lighting and optics to electronic displays to permanent magnets and guidance systems, each use requires a different element or different combination of elements.
Additionally, not all rare earth elements are found in the same types of deposits; they occur in different places and in different concentrations.
These different types of minerals are typically categorized into two subgroups based on weight:
light rare earth elements (LREE) and
heavy rare earth elements (HREE).
China's policy adds an additional subgroup, medium rare earth elements (MREE).
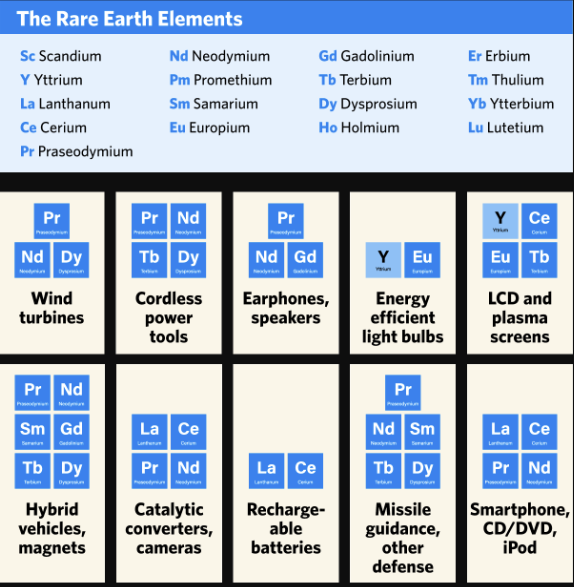
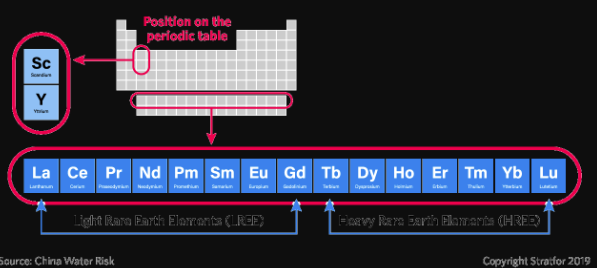
King of Rare Earths
China contains roughly a third of the world's reserves of rare earth elements, and it has only come to dominate the sector recently.
After China discovered new reserves in the 1960s, it took until the early 1990s for it to overtake the United States as the world's premier rare earth elements producer.
China's production of rare earth elements is both geographically divided by type and highly concentrated in a handful of mines.
Inner Mongolia accounts for nearly 70 percent of China's LREE production, with a single mine — Baotou Bayan Obo Mine — producing more than 50 percent of all Chinese rare earth elements.
Southern China, where HREEs were first discovered in the 1960s, accounts for most of the country's HREE production.
Jiangxi province alone produces roughly 50 percent of China's MREE and HREE, and Ganzhou city accounts for the majority of that production.
Read on to learn the rest about the relevant issues affecting the world with rare earths here
https://worldview.stratfor.com/article/ ... h-elements
Anyone can mindlessly copy tech stuff. But BigP is trying to protect his rapidly slipping Oracle status.
He has no understanding whatsoever about the practical commercial issues. The FAKE NEWS will come next.
But ignoring the struggling Oracle and back to the topic and something relevant and interesting.
The Geopolitics of Rare Earth Elements
Apr 8, 2019 | 09:00 GMT
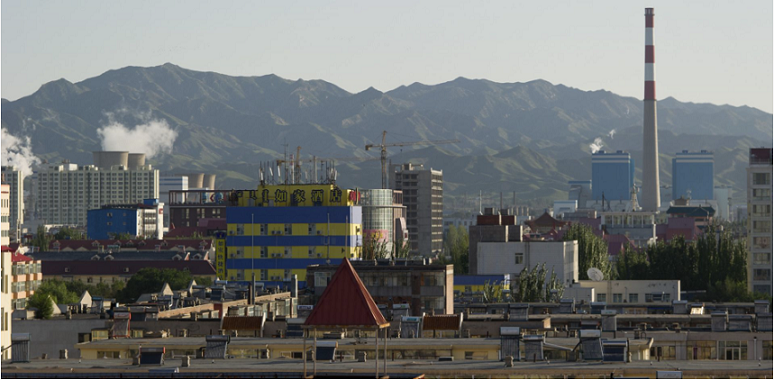
The skyline of the Inner Mongolian city of Baotou is blackened by pollution from factories processing rare earth elements, which are essential for the production of mobile phones and computers.
Pollution from factories processing rare earth elements, which are essential for the production of mobile phones and computers, blackens the skyline of Baotou, in Inner Mongolia. (Ed Jones/AFP/Getty Images)
HIGHLIGHTS
Demand for rare earth elements will grow in the next several years as the world undergoes an energy transition, but the supply chain is vulnerable.
China is the top supplier in the market, but its own growing domestic demand may lessen its dominance by driving increased production outside its own borders.
The U.S. defense industry makes up a small portion of the total demand for rare earth elements. To ensure supply alternatives from China, the U.S. government will likely need to proactively intervene in the market to shift production dependence away from China.
Editor's Note: At Stratfor, we use geopolitics to understand the constraints and advantages that geography confers on a country and the political, technological and economic decisions it compels. The exercise, taken to its logical conclusion, can extend all the way down to an atomic level. This occasional series examines the elements and the power that various combinations of protons, neutrons and electrons can exert on the world around us. In the latest installment, we look at rare earth elements.
Tucked into the sixth row of the periodic table, often represented by a single square expanded like a footnote at the bottom of the table, are the 15 lanthanides. When combined with yttrium and scandium, these materials are better known as the rare earth elements. Though they are used in very small amounts, their significance to the U.S. defense sector and to emerging and potentially disruptive technologies, combined with China's control over the majority of the market, has given the rare earth elements outsized geopolitical relevance.
The Big Picture
Each element on the periodic table tells a geopolitical story. The rare earth elements, individually and as a whole group, are the quintessential symbol for the emerging, shifting global order, as China and the United States engage in both a trade war that may soon be resolved and a tech war that will continue for decades.
The rare earth elements are already critical to the U.S. defense sector, but rare earth mining, processing and fabrication capabilities will even more strongly influence geopolitical dynamics in the coming years as the world undergoes its nascent energy transition and transportation evolution. In the near term, China will benefit from its near-monopoly, but ultimately its own growing domestic demand will limit the duration of its control over the sector and eventually force production diversification.
The Same but Different
Though they are often discussed as a group, rare earth elements have individual qualities that funnel them into specific use cases and markets. From lighting and optics to electronic displays to permanent magnets and guidance systems, each use requires a different element or different combination of elements.
Additionally, not all rare earth elements are found in the same types of deposits; they occur in different places and in different concentrations.
These different types of minerals are typically categorized into two subgroups based on weight:
light rare earth elements (LREE) and
heavy rare earth elements (HREE).
China's policy adds an additional subgroup, medium rare earth elements (MREE).
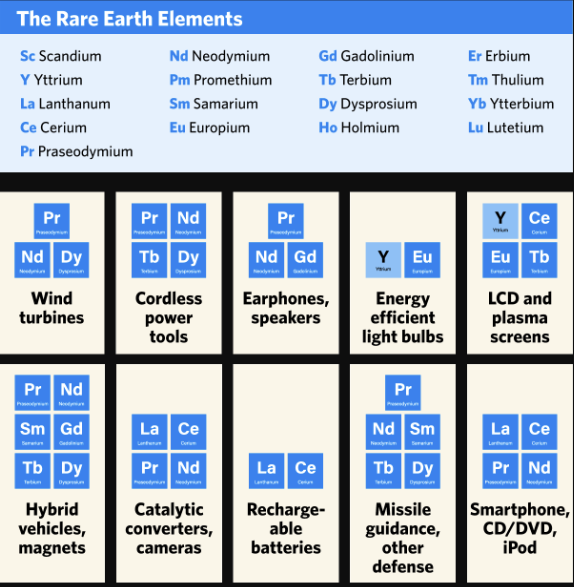
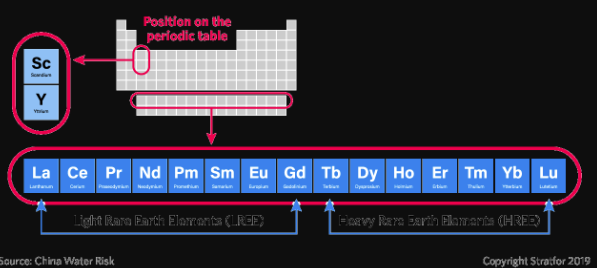
King of Rare Earths
China contains roughly a third of the world's reserves of rare earth elements, and it has only come to dominate the sector recently.
After China discovered new reserves in the 1960s, it took until the early 1990s for it to overtake the United States as the world's premier rare earth elements producer.
China's production of rare earth elements is both geographically divided by type and highly concentrated in a handful of mines.
Inner Mongolia accounts for nearly 70 percent of China's LREE production, with a single mine — Baotou Bayan Obo Mine — producing more than 50 percent of all Chinese rare earth elements.
Southern China, where HREEs were first discovered in the 1960s, accounts for most of the country's HREE production.
Jiangxi province alone produces roughly 50 percent of China's MREE and HREE, and Ganzhou city accounts for the majority of that production.
Read on to learn the rest about the relevant issues affecting the world with rare earths here
https://worldview.stratfor.com/article/ ... h-elements
- BigP
- Posts: 4970
- Joined: Mon Mar 19, 2018 3:56 pm
Re: What happens if China restricts rare earths supply ?
Rare-earth magnets are strong permanent magnets made from alloys of rare-earth elements. Developed in the 1970s and 1980s, rare-earth magnets are the strongest type of permanent magnets made, producing significantly stronger magnetic fields than other types such as ferrite or alnico magnets. The magnetic field typically produced by rare-earth magnets can exceed 1.4 teslas, whereas ferrite or ceramic magnets typically exhibit fields of 0.5 to 1 tesla.
There are two types: neodymium magnets and samarium–cobalt magnets. Rare-earth magnets are extremely brittle and also vulnerable to corrosion, so they are usually plated or coated to protect them from breaking, chipping, or crumbling into powder.
The development of rare-earth magnets began around 1966, when K. J. Strnat and G. Hoffer of the US Air Force Materials Laboratory discovered that an alloy of yttrium and cobalt, YCo5, had by far the largest magnetic anisotropy constant of any material then known.[1][2]
The term "rare earth" can be misleading, as some of these metals can be[3][4] as abundant in the Earth's crust as tin or lead,[5] but rare earth ores are unevenly distributed, not existing in seams like coal or copper, so in any given cubic kilometre of crust they are "rare". The major source is currently China.[6] Some countries classify rare earth metals as strategically important,[7] and recent Chinese export restrictions on these materials have led some to initiate research programs to develop strong magnets that do not require rare earth metals.
Neodymium magnets (small cylinders) lifting steel balls. As shown here, rare-earth magnets can easily lift thousands of times their own weight.
Contents
1 Explanation of strength
2 Magnetic properties
3 Types
3.1 Samarium-cobalt
3.2 Neodymium
4 Hazards
5 Applications
5.1 Common applications
5.2 Other applications
6 Rare-earth-free permanent magnets
7 See also
8 References
9 Further reading
10 External links
Explanation of strength
The rare-earth (lanthanide) elements are metals that are ferromagnetic, meaning that like iron they can be magnetized to become permanent magnets, but their Curie temperatures (the temperature above which their ferromagnetism disappears) are below room temperature, so in pure form their magnetism only appears at low temperatures. However, they form compounds with the transition metals such as iron, nickel, and cobalt, and some of these compounds have Curie temperatures well above room temperature. Rare-earth magnets are made from these compounds.
The greater strength of rare-earth magnets is mostly due to two factors:
First, their crystalline structures have very high magnetic anisotropy: This means that a crystal of the material preferentially magnetizes along a specific crystal axis but is very difficult to magnetize in other directions. Like other magnets, rare-earth magnets are composed of microcrystalline grains, which are aligned in a powerful magnetic field during manufacture, so their magnetic axes all point in the same direction. The resistance of the crystal lattice to turning its direction of magnetization gives these compounds a very high magnetic coercivity (resistance to being demagnetized).
Second, atoms of rare-earth elements can have high magnetic moments: Their orbital electron structures contain many unpaired electrons; in other elements, almost all of the electrons exist in pairs with opposite spins, so their magnetic fields cancel out, but in rare-earths there is much less magnetic cancellation. This is a consequence of incomplete filling of the f-shell, which can contain up to 7 unpaired electrons. In a magnet it is the unpaired electrons, aligned so they spin in the same direction, which generate the magnetic field. This gives the materials high remanence (saturation magnetization Js ). The maximal energy density B·Hmax is proportional to Js2, so these materials have the potential for storing large amounts of magnetic energy. The magnetic energy product B·Hmax of neodymium magnets is about 18 times greater than "ordinary" magnets by volume. This allows rare-earth magnets to be smaller than other magnets with the same field strength.
Magnetic properties
Some important properties used to compare permanent magnets are: remanence (Br), which measures the strength of the magnetic field; coercivity (Hci), the material's resistance to becoming demagnetized; energy product (B·Hmax), the density of magnetic energy; and Curie temperature (TC), the temperature at which the material loses its magnetism. Rare-earth magnets have higher remanence, much higher coercivity and energy product, but (for neodymium) lower Curie temperature than other types. The table below compares the magnetic performance of the two types of rare-earth magnets, neodymium (Nd2Fe14B) and samarium-cobalt (SmCo5), with other types of permanent magnets.
Magnet preparation Br
(T) Hci
(kA/m) B·Hmax
(kJ/m3) TC
(°C)
Nd2Fe14B sintered 1.0–1.4 750–2000 200–440 310–400
Nd2Fe14B bonded 0.6–0.7 600–1200 60–100 310–400
SmCo5 sintered 0.8–1.1 600–2000 120–200 720
Sm(Co,Fe,Cu,Zr)7 sintered 0.9–1.15 450–1300 150–240 800
Alnico sintered 0.6–1.4 275 10–88 700–860
Sr-ferrite sintered 0.2–0.4 100–300 10–40 450
Iron (Fe) bar magnet annealed ? 800[8] ? 770[9]
Source:[citation needed]
Types
Samarium-cobalt
Main article: Samarium–cobalt magnet
Samarium–cobalt magnets (chemical formula: SmCo5), the first family of rare-earth magnets invented, are less used than neodymium magnets because of their higher cost and lower magnetic field strength. However, samarium–cobalt has a higher Curie temperature, creating a niche for these magnets in applications where high field strength is needed at high operating temperatures. They are highly resistant to oxidation, but sintered samarium–cobalt magnets are brittle and prone to chipping and cracking and may fracture when subjected to thermal shock.
Neodymium
Main article: Neodymium magnet
Neodymium magnet with nickel plating mostly removed
Neodymium magnets, invented in the 1980s, are the strongest and most affordable type of rare-earth magnet. They are made of an alloy of neodymium, iron, and boron (Nd2Fe14B), sometimes abbreviated as NIB. Neodymium magnets are used in numerous applications requiring strong, compact permanent magnets, such as electric motors for cordless tools, hard disk drives, magnetic holddowns, and jewelry clasps. They have the highest magnetic field strength and have a higher coercivity (which makes them magnetically stable), but they have a lower Curie temperature and are more vulnerable to oxidation than samarium–cobalt magnets. Corrosion can cause unprotected magnets to spall off a surface layer or to crumble into a powder. Use of protective surface treatments such as gold, nickel, zinc, and tin plating and epoxy-resin coating can provide corrosion protection, the vast majority of neodymium magnets use nickel plating to provide a robust protection.
Originally, the high cost of these magnets limited their use to applications requiring compactness together with high field strength. Both the raw materials and the patent licenses were expensive. However, since the 1990s, NIB magnets have become steadily less expensive, and the low cost has inspired new uses such as magnetic construction toys.
Hazards
The greater force exerted by rare-earth magnets creates hazards that are not seen with other types of magnet. Magnets larger than a few centimeters are strong enough to cause injuries to body parts pinched between two magnets or a magnet and a metal surface, even causing broken bones.[10] Magnets allowed to get too near each other can strike each other with enough force to chip and shatter the brittle material, and the flying chips can cause injuries. There have even been cases where young children who have swallowed several magnets have had a fold of the digestive tract pinched between the magnets, causing injury and in one case intestinal perforations, sepsis and death.[11]
The U.S. Consumer Product Safety Commission passed a rule restricting rare-earth magnet size in consumer products, but it was vacated by a US Federal court decision in November 2016.[12]
Applications
Since their prices became competitive in the 1990s, neodymium magnets have been replacing Alnico and ferrite magnets in the many applications in modern technology requiring powerful magnets. Their greater strength allows smaller and lighter magnets to be used for a given application.
Common applications
Neodymium magnet balls
Common applications of rare-earth magnets include:
computer hard disk drives
wind turbine generators
speakers / headphones
bicycle dynamos
MRI scanners
fishing reel brakes
permanent magnet motors in cordless tools
high-performance AC servo motors
traction motors and integrated starter-generators in hybrid and electric vehicles
mechanically powered flashlights, employing rare earth magnets for generating electricity in a shaking motion or rotating (hand-crank-powered) motion
industrial uses such as maintaining product purity, equipment protection, and quality control
capture of fine metallic particles in lubricating oils (crankcases of internal combustion engines, also gearboxes and differentials), so as to keep said particles out of circulation, thereby rendering them unable to cause abrasive wear of moving machine parts
Other applications
Other applications of rare-earth magnets include:
Linear motors (used in maglev trains, etc.)
Stop motion animation: as tie-downs when the use of traditional screw and nut tie-downs is impractical.
Diamagnetic levitation experimentation, the study of magnetic field dynamics and superconductor levitation.
Electrodynamic bearings
Launched roller coaster technology found on roller coaster and other thrill rides.
LED Throwies, small LEDs attached to a button cell battery and a small rare earth magnet, used as a form of non-destructive graffiti and temporary public art.
Neodymium magnet toys
Electric guitar pickups
Miniature figures, for which rare-earth magnets have gained popularity in the miniatures gaming community for their small size and relative strength assisting in basing and swapping weapons between models.
Rare-earth-free permanent magnets
The United States Department of Energy has identified a need to find substitutes for rare-earth metals in permanent-magnet technology and has begun funding such research. The Advanced Research Projects Agency-Energy (ARPA-E) has sponsored a Rare Earth Alternatives in Critical Technologies (REACT) program, to develop alternative materials. In 2011, ARPA-E awarded 31.6 million dollars to fund Rare-Earth Substitute projects.[13]
See also
DEMETER
Recycling
References
Cullity, B. D.; Graham, C. D. (2008). Introduction to Magnetic Materials. Wiley-IEEE. p. 489. ISBN 0-471-47741-9.
Lovelace, Alan M. (March–April 1971). "More Mileage Than Programmed From Military R&D". Air University Review. US Air Force. 22 (3): 14–23. Retrieved July 4, 2012.
McCaig, Malcolm (1977). Permanent Magnets in Theory and Practice. USA: Wiley. p. 123. ISBN 0-7273-1604-4.
Sigel, Astrid; Helmut Sigel (2003). The lanthanides and their interrelations with biosystems. USA: CRC Press. pp. v. ISBN 0-8247-4245-1.
Bobber, R. J. (1981). "New Types of Transducers". Underwater Acoustics and Signal Processing. p. 243. doi:10.1007/978-94-009-8447-9_20. ISBN 978-94-009-8449-3.
Walsh, Bryan (March 13, 2012). "Raring to Fight: The U.S. Tangles with China over Rare-Earth Exports". Time Magazine. Retrieved November 13, 2017.
Chu, Steven (2011). Critical Materials Strategy. DIANE Publishing. pp. 96–98. ISBN 1437944183.
Introduction to Magnets and Magnetic Materials, David Jiles, Ames Laboratrories, US DoE, 1991
3 Sources:
Beichner and Serway. Physics for Scientists & Engineers with Modern Physics. 5th ed. Orlando: Saunders College, 2000: 963.
Curie Temperature." McGraw-Hill Encyclopedia of Science & Technology. 8th ed. 20 vols. N.P: McGraw-Hill, 1997.
Hall, H.E and J.R. Hook. Solid State Physics. 2nd ed. Chichester: John Wiley & Sons Ltd, 1991: 226.
Swain, Frank (March 6, 2009). "How to remove a finger with two super magnets". The Sciencepunk Blog. Seed Media Group LLC. Retrieved 2017-11-01.
"Magnet Safety Alert" (PDF). U.S. Consumer Product Safety Commission. Retrieved 20 July 2014.
"CPSC Recall Snapshot" (PDF). Alston & Bird. December 2016.
"Research Funding for Rare Earth Free Permanent Magnets". ARPA-E. Retrieved 23 April 2013.
Further reading
Edward P. Furlani, "Permanent Magnet and Electromechanical Devices: Materials, Analysis and Applications", Academic Press Series in Electromagnetism (2001). ISBN 0-12-269951-3.
Peter Campbell, "Permanent Magnet Materials and their Application" (Cambridge Studies in Magnetism)(1996). ISBN 978-0-521-56688-9.
Brown, D. N.; B. Smith; B. M. Ma; P. Campbell (2004). "The Dependence of Magnetic Properties and Hot Workability of Rare Earth-Iron-Boride Magnets Upon Composition" (PDF). IEEE Transactions on Magnetics. 40 (4): 2895–2897. Bibcode:2004ITM....40.2895B. doi:10.1109/TMAG.2004.832240. ISSN 0018-9464. Archived from the original (PDF) on 2012-04-25.
External links
Standard Specifications for Permanent Magnet Materials (Magnetic Materials Producers Association)
Edwards, Lin (22 March 2010). "Iron-nitrogen compound forms strongest magnet known". PhysOrg.
Categories: Magnetic levitationTypes of magnetsFerromagnetic materialsLoudspeakers
Navigation menu
Not logged inTalkContributionsCreate accountLog inArticleTalkReadEditView historySearch
Search Wikipedia
Main page
Contents
Featured content
Current events
Random article
Donate to Wikipedia
Wikipedia store
Interaction
Help
About Wikipedia
Community portal
Recent changes
Contact page
Tools
What links here
Related changes
Upload file
Special pages
Permanent link
Page information
Wikidata item
Cite this page
Print/export
Create a book
Download as PDF
Printable version
Languages
العربية
Deutsch
Español
Français
Nederlands
日本語
Русский
Tiếng Việt
中文
4 more
Edit links
This page was last edited on 24 November 2019, at 07:08 (UTC).
Text is available under the Creative Commons Attribution-ShareAlike License; additional terms may apply. By using this site, you agree to the Terms of Use and Privacy Policy. Wikipedia® is a registered trademark of the Wikimedia Foundation, Inc., a non-profit organization.
There are two types: neodymium magnets and samarium–cobalt magnets. Rare-earth magnets are extremely brittle and also vulnerable to corrosion, so they are usually plated or coated to protect them from breaking, chipping, or crumbling into powder.
The development of rare-earth magnets began around 1966, when K. J. Strnat and G. Hoffer of the US Air Force Materials Laboratory discovered that an alloy of yttrium and cobalt, YCo5, had by far the largest magnetic anisotropy constant of any material then known.[1][2]
The term "rare earth" can be misleading, as some of these metals can be[3][4] as abundant in the Earth's crust as tin or lead,[5] but rare earth ores are unevenly distributed, not existing in seams like coal or copper, so in any given cubic kilometre of crust they are "rare". The major source is currently China.[6] Some countries classify rare earth metals as strategically important,[7] and recent Chinese export restrictions on these materials have led some to initiate research programs to develop strong magnets that do not require rare earth metals.
Neodymium magnets (small cylinders) lifting steel balls. As shown here, rare-earth magnets can easily lift thousands of times their own weight.
Contents
1 Explanation of strength
2 Magnetic properties
3 Types
3.1 Samarium-cobalt
3.2 Neodymium
4 Hazards
5 Applications
5.1 Common applications
5.2 Other applications
6 Rare-earth-free permanent magnets
7 See also
8 References
9 Further reading
10 External links
Explanation of strength
The rare-earth (lanthanide) elements are metals that are ferromagnetic, meaning that like iron they can be magnetized to become permanent magnets, but their Curie temperatures (the temperature above which their ferromagnetism disappears) are below room temperature, so in pure form their magnetism only appears at low temperatures. However, they form compounds with the transition metals such as iron, nickel, and cobalt, and some of these compounds have Curie temperatures well above room temperature. Rare-earth magnets are made from these compounds.
The greater strength of rare-earth magnets is mostly due to two factors:
First, their crystalline structures have very high magnetic anisotropy: This means that a crystal of the material preferentially magnetizes along a specific crystal axis but is very difficult to magnetize in other directions. Like other magnets, rare-earth magnets are composed of microcrystalline grains, which are aligned in a powerful magnetic field during manufacture, so their magnetic axes all point in the same direction. The resistance of the crystal lattice to turning its direction of magnetization gives these compounds a very high magnetic coercivity (resistance to being demagnetized).
Second, atoms of rare-earth elements can have high magnetic moments: Their orbital electron structures contain many unpaired electrons; in other elements, almost all of the electrons exist in pairs with opposite spins, so their magnetic fields cancel out, but in rare-earths there is much less magnetic cancellation. This is a consequence of incomplete filling of the f-shell, which can contain up to 7 unpaired electrons. In a magnet it is the unpaired electrons, aligned so they spin in the same direction, which generate the magnetic field. This gives the materials high remanence (saturation magnetization Js ). The maximal energy density B·Hmax is proportional to Js2, so these materials have the potential for storing large amounts of magnetic energy. The magnetic energy product B·Hmax of neodymium magnets is about 18 times greater than "ordinary" magnets by volume. This allows rare-earth magnets to be smaller than other magnets with the same field strength.
Magnetic properties
Some important properties used to compare permanent magnets are: remanence (Br), which measures the strength of the magnetic field; coercivity (Hci), the material's resistance to becoming demagnetized; energy product (B·Hmax), the density of magnetic energy; and Curie temperature (TC), the temperature at which the material loses its magnetism. Rare-earth magnets have higher remanence, much higher coercivity and energy product, but (for neodymium) lower Curie temperature than other types. The table below compares the magnetic performance of the two types of rare-earth magnets, neodymium (Nd2Fe14B) and samarium-cobalt (SmCo5), with other types of permanent magnets.
Magnet preparation Br
(T) Hci
(kA/m) B·Hmax
(kJ/m3) TC
(°C)
Nd2Fe14B sintered 1.0–1.4 750–2000 200–440 310–400
Nd2Fe14B bonded 0.6–0.7 600–1200 60–100 310–400
SmCo5 sintered 0.8–1.1 600–2000 120–200 720
Sm(Co,Fe,Cu,Zr)7 sintered 0.9–1.15 450–1300 150–240 800
Alnico sintered 0.6–1.4 275 10–88 700–860
Sr-ferrite sintered 0.2–0.4 100–300 10–40 450
Iron (Fe) bar magnet annealed ? 800[8] ? 770[9]
Source:[citation needed]
Types
Samarium-cobalt
Main article: Samarium–cobalt magnet
Samarium–cobalt magnets (chemical formula: SmCo5), the first family of rare-earth magnets invented, are less used than neodymium magnets because of their higher cost and lower magnetic field strength. However, samarium–cobalt has a higher Curie temperature, creating a niche for these magnets in applications where high field strength is needed at high operating temperatures. They are highly resistant to oxidation, but sintered samarium–cobalt magnets are brittle and prone to chipping and cracking and may fracture when subjected to thermal shock.
Neodymium
Main article: Neodymium magnet
Neodymium magnet with nickel plating mostly removed
Neodymium magnets, invented in the 1980s, are the strongest and most affordable type of rare-earth magnet. They are made of an alloy of neodymium, iron, and boron (Nd2Fe14B), sometimes abbreviated as NIB. Neodymium magnets are used in numerous applications requiring strong, compact permanent magnets, such as electric motors for cordless tools, hard disk drives, magnetic holddowns, and jewelry clasps. They have the highest magnetic field strength and have a higher coercivity (which makes them magnetically stable), but they have a lower Curie temperature and are more vulnerable to oxidation than samarium–cobalt magnets. Corrosion can cause unprotected magnets to spall off a surface layer or to crumble into a powder. Use of protective surface treatments such as gold, nickel, zinc, and tin plating and epoxy-resin coating can provide corrosion protection, the vast majority of neodymium magnets use nickel plating to provide a robust protection.
Originally, the high cost of these magnets limited their use to applications requiring compactness together with high field strength. Both the raw materials and the patent licenses were expensive. However, since the 1990s, NIB magnets have become steadily less expensive, and the low cost has inspired new uses such as magnetic construction toys.
Hazards
The greater force exerted by rare-earth magnets creates hazards that are not seen with other types of magnet. Magnets larger than a few centimeters are strong enough to cause injuries to body parts pinched between two magnets or a magnet and a metal surface, even causing broken bones.[10] Magnets allowed to get too near each other can strike each other with enough force to chip and shatter the brittle material, and the flying chips can cause injuries. There have even been cases where young children who have swallowed several magnets have had a fold of the digestive tract pinched between the magnets, causing injury and in one case intestinal perforations, sepsis and death.[11]
The U.S. Consumer Product Safety Commission passed a rule restricting rare-earth magnet size in consumer products, but it was vacated by a US Federal court decision in November 2016.[12]
Applications
Since their prices became competitive in the 1990s, neodymium magnets have been replacing Alnico and ferrite magnets in the many applications in modern technology requiring powerful magnets. Their greater strength allows smaller and lighter magnets to be used for a given application.
Common applications
Neodymium magnet balls
Common applications of rare-earth magnets include:
computer hard disk drives
wind turbine generators
speakers / headphones
bicycle dynamos
MRI scanners
fishing reel brakes
permanent magnet motors in cordless tools
high-performance AC servo motors
traction motors and integrated starter-generators in hybrid and electric vehicles
mechanically powered flashlights, employing rare earth magnets for generating electricity in a shaking motion or rotating (hand-crank-powered) motion
industrial uses such as maintaining product purity, equipment protection, and quality control
capture of fine metallic particles in lubricating oils (crankcases of internal combustion engines, also gearboxes and differentials), so as to keep said particles out of circulation, thereby rendering them unable to cause abrasive wear of moving machine parts
Other applications
Other applications of rare-earth magnets include:
Linear motors (used in maglev trains, etc.)
Stop motion animation: as tie-downs when the use of traditional screw and nut tie-downs is impractical.
Diamagnetic levitation experimentation, the study of magnetic field dynamics and superconductor levitation.
Electrodynamic bearings
Launched roller coaster technology found on roller coaster and other thrill rides.
LED Throwies, small LEDs attached to a button cell battery and a small rare earth magnet, used as a form of non-destructive graffiti and temporary public art.
Neodymium magnet toys
Electric guitar pickups
Miniature figures, for which rare-earth magnets have gained popularity in the miniatures gaming community for their small size and relative strength assisting in basing and swapping weapons between models.
Rare-earth-free permanent magnets
The United States Department of Energy has identified a need to find substitutes for rare-earth metals in permanent-magnet technology and has begun funding such research. The Advanced Research Projects Agency-Energy (ARPA-E) has sponsored a Rare Earth Alternatives in Critical Technologies (REACT) program, to develop alternative materials. In 2011, ARPA-E awarded 31.6 million dollars to fund Rare-Earth Substitute projects.[13]
See also
DEMETER
Recycling
References
Cullity, B. D.; Graham, C. D. (2008). Introduction to Magnetic Materials. Wiley-IEEE. p. 489. ISBN 0-471-47741-9.
Lovelace, Alan M. (March–April 1971). "More Mileage Than Programmed From Military R&D". Air University Review. US Air Force. 22 (3): 14–23. Retrieved July 4, 2012.
McCaig, Malcolm (1977). Permanent Magnets in Theory and Practice. USA: Wiley. p. 123. ISBN 0-7273-1604-4.
Sigel, Astrid; Helmut Sigel (2003). The lanthanides and their interrelations with biosystems. USA: CRC Press. pp. v. ISBN 0-8247-4245-1.
Bobber, R. J. (1981). "New Types of Transducers". Underwater Acoustics and Signal Processing. p. 243. doi:10.1007/978-94-009-8447-9_20. ISBN 978-94-009-8449-3.
Walsh, Bryan (March 13, 2012). "Raring to Fight: The U.S. Tangles with China over Rare-Earth Exports". Time Magazine. Retrieved November 13, 2017.
Chu, Steven (2011). Critical Materials Strategy. DIANE Publishing. pp. 96–98. ISBN 1437944183.
Introduction to Magnets and Magnetic Materials, David Jiles, Ames Laboratrories, US DoE, 1991
3 Sources:
Beichner and Serway. Physics for Scientists & Engineers with Modern Physics. 5th ed. Orlando: Saunders College, 2000: 963.
Curie Temperature." McGraw-Hill Encyclopedia of Science & Technology. 8th ed. 20 vols. N.P: McGraw-Hill, 1997.
Hall, H.E and J.R. Hook. Solid State Physics. 2nd ed. Chichester: John Wiley & Sons Ltd, 1991: 226.
Swain, Frank (March 6, 2009). "How to remove a finger with two super magnets". The Sciencepunk Blog. Seed Media Group LLC. Retrieved 2017-11-01.
"Magnet Safety Alert" (PDF). U.S. Consumer Product Safety Commission. Retrieved 20 July 2014.
"CPSC Recall Snapshot" (PDF). Alston & Bird. December 2016.
"Research Funding for Rare Earth Free Permanent Magnets". ARPA-E. Retrieved 23 April 2013.
Further reading
Edward P. Furlani, "Permanent Magnet and Electromechanical Devices: Materials, Analysis and Applications", Academic Press Series in Electromagnetism (2001). ISBN 0-12-269951-3.
Peter Campbell, "Permanent Magnet Materials and their Application" (Cambridge Studies in Magnetism)(1996). ISBN 978-0-521-56688-9.
Brown, D. N.; B. Smith; B. M. Ma; P. Campbell (2004). "The Dependence of Magnetic Properties and Hot Workability of Rare Earth-Iron-Boride Magnets Upon Composition" (PDF). IEEE Transactions on Magnetics. 40 (4): 2895–2897. Bibcode:2004ITM....40.2895B. doi:10.1109/TMAG.2004.832240. ISSN 0018-9464. Archived from the original (PDF) on 2012-04-25.
External links
Standard Specifications for Permanent Magnet Materials (Magnetic Materials Producers Association)
Edwards, Lin (22 March 2010). "Iron-nitrogen compound forms strongest magnet known". PhysOrg.
Categories: Magnetic levitationTypes of magnetsFerromagnetic materialsLoudspeakers
Navigation menu
Not logged inTalkContributionsCreate accountLog inArticleTalkReadEditView historySearch
Search Wikipedia
Main page
Contents
Featured content
Current events
Random article
Donate to Wikipedia
Wikipedia store
Interaction
Help
About Wikipedia
Community portal
Recent changes
Contact page
Tools
What links here
Related changes
Upload file
Special pages
Permanent link
Page information
Wikidata item
Cite this page
Print/export
Create a book
Download as PDF
Printable version
Languages
العربية
Deutsch
Español
Français
Nederlands
日本語
Русский
Tiếng Việt
中文
4 more
Edit links
This page was last edited on 24 November 2019, at 07:08 (UTC).
Text is available under the Creative Commons Attribution-ShareAlike License; additional terms may apply. By using this site, you agree to the Terms of Use and Privacy Policy. Wikipedia® is a registered trademark of the Wikimedia Foundation, Inc., a non-profit organization.
- BigP
- Posts: 4970
- Joined: Mon Mar 19, 2018 3:56 pm
Re: What happens if China restricts rare earths supply ?
Neodymium is a chemical element. Its official symbol is Nd, and its atomic number is 60, which means it has 60 protons in its nucleus.
Elemental neodymium
On the periodic table of elements, neodymium is represented by the symbol Nd. It has an atomic number of 60 because it has 60 protons in its nucleus.
M-tic magnetic construction toy, © fir0002, CC BY-NC 3.0
The element was discovered by Austrian chemist Baron Carl Auervon Welsbach in a roundabout way. Welsbach’s original elemental ‘discovery’ was didymium – a material he thought was an element. It even had the symbol Di in Mendeleev’s 1869 version of the periodic table of elements. Welsbach later separated the material into two elements – neodymium and praseodymium. The name neodymium comes from the Greek word neos (meaning new) and didymos (meaning twin). Praseodymium means green twin. The elements are so similar that they are next to each other on the periodic table.
Rare-earth elements
Neodymium is one of the 17 elements known as rare-earth elements. The rare-earth elements occur together on the periodic table. Fifteen of the elements, numbered 57–71, are in the row that sits under the main table. (This row is also called the lanthanide series.) Two more elements – scandium and yttrium – have similar chemical properties so they are also called rare-earth elements.
The rare-earth elements aren’t really all that rare. In the 18th and 19th centuries, materials were called ‘earths’ if they could not be changed further by heating them up. ‘Earths’ like magnesium were relatively easy to find. The rare-earth elements are dispersed or ‘sprinkled’ in ore deposits, rather than occurring as free elements or concentrated in minerals. At the time, they were difficult to locate so they were considered rare.
Neodymium is fairly common – it’s about as abundant as zinc and copper. However, it is dispersed throughout the Earth’s crust, with small amounts found here and there. Neodymium, like most rare-earth elements, is often a byproduct from other mining operations. If it is found with other rare-earth elements that are chemically similar, it becomes a complex process and a considerable expense to separate them. In 2019, a metric ton of neodymium oxide costs more than NZ$160,000! Compare that to NZ$4,000 for zinc and NZ$10,000 for copper. In spite of the price, neodymium and other rare-earth elements are in huge demand.
Welding goggles
Welding goggles protect the eyes from heat, debris and optical radiation. A mixture of neodymium and praseodymium salts is used to colour the glass.
Uses of neodymium
Neodymium compounds were first used to colour glass. Its properties cause the colour of the glass to change from purple to yellow to blue or green under different lighting conditions. We still use neodymium compounds in glass products today – to whiten the light in incandescent bulbs and to make goggles for welders and glass blowers.
The real demands for neodymium are in products likely to be found in your pocket and throughout the classroom. Neodymium, iron and boron (NIB) combine to create very powerful magnets. A 1 g NIB magnet can hold up a 1.3 kg iron sphere! Tiny NIB magnets are found in cell phones, earbuds, computer hard drives and DVD and CD players. Larger NIB magnets are used in the electric motors of hybrid and electric vehicles and in some wind turbines. NIB magnets are also used to identify counterfeit money. Real paper money has tiny magnetic particles added to the inks when they are printed.
Neodymium magnets
The element neodymium combines with iron and boron to create powerful permanent magnets. The lightweight yet strong magnets have many uses in modern technology.
NIB magnets and toys
Neodymium magnets are exceptionally strong. They have a very strong attraction to one another and can move considerable distances and at great speed. There are reports that people have had fingers crushed when caught between two magnets.
Magnetic building sets with rods and balls have been redesigned to make them safer to use. The tiny, strong neodymium magnets make the building sets lots of fun, but if the magnets come loose, they can be dangerous if swallowed. The magnets attract each other and can cause tears in the stomach and intestines.
Nature of Technology
Rare-earth elements are difficult to mine and process. Their production requires careful management to minimise the associated environmental hazards. Only a few countries mine and process rare-earth elements. As the demand grows, supply has – at times – become a political issue.
One solution is to recover and reuse rare-earth materials from cell phones, hard drives and other electronic devices. The technology to recycle rare-earth materials is becoming more efficient and cost-effective. This will allow the materials to be processed on much larger scales.
Related collection
The Science Learning Hub team has curated a collection of resources related to the periodic table of elements. Log in to make this collection part of your private collection, just click on the copy icon. You can then add additional content and notes and make other changes. Registering an account for the Science Learning Hub is easy and free – sign up with your email address or Google account. Look for the Sign in button at the top of each page.
Useful links
Rare opportunity to recycle rare earths discusses some of the issues and technology involved with rare-earth production and recycling.
This article from Investorintel includes a timeline of events regarding the production and export of rare-earth elements.
Save
Published 26 July 2019 Referencing Hub articles
View related content below
Explore related articles
ARTICLE
Limestone as an oil reservoir
The world’s largest oil fields are contained in limestones. By contrast, New Zealand’s oil deposits are mostly sandstone based. However, limestone associated with the Tikorangi ...
READ MORE
STAR
ARTICLE
Riparian restoration
Riparian zones are the areas beside streams. These areas are sometimes reconstructed or improved to provide habitat for fish and other aquatic life and to stabilise banks against erosion. This ...
READ MORE
STAR
ARTICLE
Bioplastics
Bioplastics are plastic materials that are either biodegradable or derived from renewable resources or both. Currently, petrochemical-based plastics make up 99% of the plastics market. However ...
READ MORE
STAR
Explore related activities
ACTIVITY
Testing the degradability of potato plates
In this activity, students compare the rate of degradation of disposable plates using three different disposal methods. Purpose To experiment with a range of disposable plates made from different ...
READ MORE
STAR
ACTIVITY
Promoting potato plates
In this activity, students use their knowledge of potato plates to write a letter promoting their use. Purpose This activity will help students understand product lifecycles and compare the ...
READ MORE
STAR
ACTIVITY
Responding to Rena
In this activity, students consider short-term and long-term responses to an environmental disaster such as the Rena. By the end of this activity, students should be able to: describe ...
READ MORE
STAR
Explore related PLD
TEACHER PLD
Designing a new product from potato starch – unit plan
Students develop their knowledge to design a disposable product as a sustainable alternative to an existing product. Purpose To consider the issues of increasing plastics use and ...
READ MORE
STAR
TEACHER PLD
Marketing a reusable product: potato plates – unit plan
Students develop their knowledge to design a disposable product as a sustainable alternative to an existing product. Purpose To understand why increasing use of non-degradable ...
READ MORE
STAR
TEACHER PLD
An introduction to Aqua Republica
Gaming to understand the complexities of water catchment management Explore the inaugural New Zealand Aqua Republica Eco Challenge 2016 with Deli Connell, Andrea Soanes and ...
READ MORE
STAR
Explore related videos
VIDEO
Oil formation
This animated video demonstrates the formation of hydrocarbons over millions of years in the depths of the Earth. Oil and gas forms in sedimentary ocean basins. Dead plankton (organic plant ...
READ MORE
STAR
VIDEO
Oil and gas in rocks
Adam Vonk explains that, to find hydrocarbons, scientists first need to identify a source rock that has been buried deep enough so that the temperature and pressure drive off or ...
READ MORE
STAR
VIDEO
Rotorua geothermal field: protecting a taonga
Rotorua is world famous for its geothermal features. For generations, local Māori used the hot pools with little impact on the natural system. As Rotorua’s population grew ...
READ MORE
STAR
Explore related interactives
INTERACTIVE
Temperature – the hot and the cold
This interactive highlights the critical role temperature plays in the world of ceramics.
READ MORE
STAR
INTERACTIVE
O-Sialon production
This interactive shows the process of creating an advanced ceramic, O-Sialon, in the laboratory.
READ MORE
STAR
INTERACTIVE
Dynamic and complex: the global water cycle
Water in the Earth system is influencing all aspects of life on Earth. Pathways, storage, transfers and transformations have an effect on the global climate and human welfare. Within this ...
READ MORE
STAR
Twitter
Pinterest
Facebook
Instagram
Email Us
Your email address
Read our latest newsletter online here.
Events
About
Contact us
Privacy
Copyright
Help
Curious Minds is a Government initiative jointly led by the Ministry of Business, Innovation and Employment, the Ministry of Education and the Office of the Prime Minister’s Chief Science Advisor.
Science Learning Hub – Pokapū Akoranga Pūtaiao © 2007-2019 The University of Waikato Te Whare Wānan
Elemental neodymium
On the periodic table of elements, neodymium is represented by the symbol Nd. It has an atomic number of 60 because it has 60 protons in its nucleus.
M-tic magnetic construction toy, © fir0002, CC BY-NC 3.0
The element was discovered by Austrian chemist Baron Carl Auervon Welsbach in a roundabout way. Welsbach’s original elemental ‘discovery’ was didymium – a material he thought was an element. It even had the symbol Di in Mendeleev’s 1869 version of the periodic table of elements. Welsbach later separated the material into two elements – neodymium and praseodymium. The name neodymium comes from the Greek word neos (meaning new) and didymos (meaning twin). Praseodymium means green twin. The elements are so similar that they are next to each other on the periodic table.
Rare-earth elements
Neodymium is one of the 17 elements known as rare-earth elements. The rare-earth elements occur together on the periodic table. Fifteen of the elements, numbered 57–71, are in the row that sits under the main table. (This row is also called the lanthanide series.) Two more elements – scandium and yttrium – have similar chemical properties so they are also called rare-earth elements.
The rare-earth elements aren’t really all that rare. In the 18th and 19th centuries, materials were called ‘earths’ if they could not be changed further by heating them up. ‘Earths’ like magnesium were relatively easy to find. The rare-earth elements are dispersed or ‘sprinkled’ in ore deposits, rather than occurring as free elements or concentrated in minerals. At the time, they were difficult to locate so they were considered rare.
Neodymium is fairly common – it’s about as abundant as zinc and copper. However, it is dispersed throughout the Earth’s crust, with small amounts found here and there. Neodymium, like most rare-earth elements, is often a byproduct from other mining operations. If it is found with other rare-earth elements that are chemically similar, it becomes a complex process and a considerable expense to separate them. In 2019, a metric ton of neodymium oxide costs more than NZ$160,000! Compare that to NZ$4,000 for zinc and NZ$10,000 for copper. In spite of the price, neodymium and other rare-earth elements are in huge demand.
Welding goggles
Welding goggles protect the eyes from heat, debris and optical radiation. A mixture of neodymium and praseodymium salts is used to colour the glass.
Uses of neodymium
Neodymium compounds were first used to colour glass. Its properties cause the colour of the glass to change from purple to yellow to blue or green under different lighting conditions. We still use neodymium compounds in glass products today – to whiten the light in incandescent bulbs and to make goggles for welders and glass blowers.
The real demands for neodymium are in products likely to be found in your pocket and throughout the classroom. Neodymium, iron and boron (NIB) combine to create very powerful magnets. A 1 g NIB magnet can hold up a 1.3 kg iron sphere! Tiny NIB magnets are found in cell phones, earbuds, computer hard drives and DVD and CD players. Larger NIB magnets are used in the electric motors of hybrid and electric vehicles and in some wind turbines. NIB magnets are also used to identify counterfeit money. Real paper money has tiny magnetic particles added to the inks when they are printed.
Neodymium magnets
The element neodymium combines with iron and boron to create powerful permanent magnets. The lightweight yet strong magnets have many uses in modern technology.
NIB magnets and toys
Neodymium magnets are exceptionally strong. They have a very strong attraction to one another and can move considerable distances and at great speed. There are reports that people have had fingers crushed when caught between two magnets.
Magnetic building sets with rods and balls have been redesigned to make them safer to use. The tiny, strong neodymium magnets make the building sets lots of fun, but if the magnets come loose, they can be dangerous if swallowed. The magnets attract each other and can cause tears in the stomach and intestines.
Nature of Technology
Rare-earth elements are difficult to mine and process. Their production requires careful management to minimise the associated environmental hazards. Only a few countries mine and process rare-earth elements. As the demand grows, supply has – at times – become a political issue.
One solution is to recover and reuse rare-earth materials from cell phones, hard drives and other electronic devices. The technology to recycle rare-earth materials is becoming more efficient and cost-effective. This will allow the materials to be processed on much larger scales.
Related collection
The Science Learning Hub team has curated a collection of resources related to the periodic table of elements. Log in to make this collection part of your private collection, just click on the copy icon. You can then add additional content and notes and make other changes. Registering an account for the Science Learning Hub is easy and free – sign up with your email address or Google account. Look for the Sign in button at the top of each page.
Useful links
Rare opportunity to recycle rare earths discusses some of the issues and technology involved with rare-earth production and recycling.
This article from Investorintel includes a timeline of events regarding the production and export of rare-earth elements.
Save
Published 26 July 2019 Referencing Hub articles
View related content below
Explore related articles
ARTICLE
Limestone as an oil reservoir
The world’s largest oil fields are contained in limestones. By contrast, New Zealand’s oil deposits are mostly sandstone based. However, limestone associated with the Tikorangi ...
READ MORE
STAR
ARTICLE
Riparian restoration
Riparian zones are the areas beside streams. These areas are sometimes reconstructed or improved to provide habitat for fish and other aquatic life and to stabilise banks against erosion. This ...
READ MORE
STAR
ARTICLE
Bioplastics
Bioplastics are plastic materials that are either biodegradable or derived from renewable resources or both. Currently, petrochemical-based plastics make up 99% of the plastics market. However ...
READ MORE
STAR
Explore related activities
ACTIVITY
Testing the degradability of potato plates
In this activity, students compare the rate of degradation of disposable plates using three different disposal methods. Purpose To experiment with a range of disposable plates made from different ...
READ MORE
STAR
ACTIVITY
Promoting potato plates
In this activity, students use their knowledge of potato plates to write a letter promoting their use. Purpose This activity will help students understand product lifecycles and compare the ...
READ MORE
STAR
ACTIVITY
Responding to Rena
In this activity, students consider short-term and long-term responses to an environmental disaster such as the Rena. By the end of this activity, students should be able to: describe ...
READ MORE
STAR
Explore related PLD
TEACHER PLD
Designing a new product from potato starch – unit plan
Students develop their knowledge to design a disposable product as a sustainable alternative to an existing product. Purpose To consider the issues of increasing plastics use and ...
READ MORE
STAR
TEACHER PLD
Marketing a reusable product: potato plates – unit plan
Students develop their knowledge to design a disposable product as a sustainable alternative to an existing product. Purpose To understand why increasing use of non-degradable ...
READ MORE
STAR
TEACHER PLD
An introduction to Aqua Republica
Gaming to understand the complexities of water catchment management Explore the inaugural New Zealand Aqua Republica Eco Challenge 2016 with Deli Connell, Andrea Soanes and ...
READ MORE
STAR
Explore related videos
VIDEO
Oil formation
This animated video demonstrates the formation of hydrocarbons over millions of years in the depths of the Earth. Oil and gas forms in sedimentary ocean basins. Dead plankton (organic plant ...
READ MORE
STAR
VIDEO
Oil and gas in rocks
Adam Vonk explains that, to find hydrocarbons, scientists first need to identify a source rock that has been buried deep enough so that the temperature and pressure drive off or ...
READ MORE
STAR
VIDEO
Rotorua geothermal field: protecting a taonga
Rotorua is world famous for its geothermal features. For generations, local Māori used the hot pools with little impact on the natural system. As Rotorua’s population grew ...
READ MORE
STAR
Explore related interactives
INTERACTIVE
Temperature – the hot and the cold
This interactive highlights the critical role temperature plays in the world of ceramics.
READ MORE
STAR
INTERACTIVE
O-Sialon production
This interactive shows the process of creating an advanced ceramic, O-Sialon, in the laboratory.
READ MORE
STAR
INTERACTIVE
Dynamic and complex: the global water cycle
Water in the Earth system is influencing all aspects of life on Earth. Pathways, storage, transfers and transformations have an effect on the global climate and human welfare. Within this ...
READ MORE
STAR
Email Us
Your email address
Read our latest newsletter online here.
Events
About
Contact us
Privacy
Copyright
Help
Curious Minds is a Government initiative jointly led by the Ministry of Business, Innovation and Employment, the Ministry of Education and the Office of the Prime Minister’s Chief Science Advisor.
Science Learning Hub – Pokapū Akoranga Pūtaiao © 2007-2019 The University of Waikato Te Whare Wānan
-
- Posts: 1355
- Joined: Wed Dec 28, 2016 10:56 am
Re: What happens if China restricts rare earths supply ?
Now the BigP Oracle is panicking as his Oracle status slowly slips away.
His hysterical attempts at SPAMMING to try to appear knowledgeable are sad to observe. Any fool can copy Wikileaks etc without understanding a single word.
He is decomposing slowly into a blubbering heap.
The FAKE NEWS will come next.
He really needs to be spanked like a naughty child.
His hysterical attempts at SPAMMING to try to appear knowledgeable are sad to observe. Any fool can copy Wikileaks etc without understanding a single word.
He is decomposing slowly into a blubbering heap.
The FAKE NEWS will come next.
He really needs to be spanked like a naughty child.
- BigP
- Posts: 4970
- Joined: Mon Mar 19, 2018 3:56 pm
Re: What happens if China restricts rare earths supply ?
Oh dear!!!!!!!!!!!!!!!!!Juliar wrote: ↑Mon Dec 16, 2019 7:25 pmNow the BigP Oracle is panicking as his Oracle status slowly slips away.
His hysterical attempts at SPAMMING to try to appear knowledgeable are sad to observe. Any fool can copy Wikileaks etc without understanding a single word.
He is decomposing slowly into a blubbering heap.
The FAKE NEWS will come next.
He really needs to be spanked like a naughty child.
Rhodium is a silver-white metallic element that is highly reflective and resistant to corrosion. It is considered the rarest and most valuable precious metal in the world — well above gold or silver. The name rhodium comes from the Greek word "rhodon," meaning rose, named for the rose-red color of its salts.
Just the facts
Atomic number (number of protons in the nucleus): 45
Atomic symbol (on the periodic table of the elements): Rh
Atomic weight (average mass of the atom): 102.90550
Density: 12.41 grams per cubic centimeter
Phase at room temperature: Solid
Melting point: 3,567 degrees F (1,964 degrees C)
Boiling point: 6,683 degrees F (3,695 degrees C)
Number of isotopes (atoms of the same element with a different number of neutrons): 24 whose half-lives are known; one stable
Most common isotopes: One stable isotope Rh-103
Properties
Rhodium is one of the of the six platinum group metals: platinum, palladium, rhodium, osmium, iridium and ruthenium. It is also classified as a noble metal, meaning that it does not react to oxygen easily, acts as a fantastic catalyst and is resistant to corrosion and oxidation. Some common characteristics of the platinum group metals include high melting points, general non-toxicity, and resistance to wear, oxidation and corrosion, according to Chemistry Libretexts.
Rhodium is the rarest of the platinum group, only occurring up to one part per 200 million in the Earth's crust, according to Chemistry Libretexts. Rhodium has lower density and a higher melting point than platinum. Rhodium it is unaffected by air and water up to 1,112 degrees Fahrenheit (600 degrees Celsius), according to Lenntech.
Electron configuration and elemental properties of rhodium.
Electron configuration and elemental properties of rhodium. (Image credit: Greg Robson/Creative Commons, Andrei Marincas Shutterstock)
Discovery
Rhodium was discovered in 1803 by English chemist William Hyde Wollaston shortly after he had discovered the element palladium. Wollaston extracted rhodium from a piece of platinum ore that he had obtained from South America. Rhodium often occurs with deposits of platinum and is commonly obtained from the mining and refining of platinum.
Wollaston was first alerted to the possibility of a new element existing in platinum ore by the French chemist Hippolyte-Victor Collet-Descotils, who believed that the red color of some platinum salts was due to the presence of an unidentified metal. After a series of chemical reactions, Wollaston was able to remove the platinum and palladium from the sample of platinum ore. He was left with a dark red powder — which turned out to be sodium rhodium chloride, according to Jefferson Lab.
Uses
The main use for rhodium is in catalytic converters designed to clean vehicle emissions. Rhodium — often together with palladium and/or platinum — accomplishes this by reducing nitrogen oxide in exhaust gas. Without rhodium catalysts, the air in our cities would be much worse due to vehicle exhausts.
Since rhodium is quite brilliant and resistant to tarnishing, it is used as a finish for jewelry, searchlights and mirrors. It is also alloyed with platinum for aircraft turbine engines. In the chemical industry, rhodium is used as a catalyst in the making of nitric acid, acetic acid and hydrogenation reactions, according to the Royal Society of Chemistry (RSC).Other uses for rhodium are coating optic fibers, crucibles, thermocouple elements and headlight reflectors. Since it has a low electrical resistance and is highly resistant to corrosion, it is used as an electrical contact material as well, according to RSC.
Rhodium is often alloyed with platinum and iridium to make an oxidation-resistant metal that can stand against high temperatures. These alloys are used in furnace windings, pen nibs, phonograph needles, high-temperature thermocouple and resistance wires, electrodes for aircraft spark plugs, bearings and electrical contacts, according toLenntech.
Rhodium has no known biological use and no known use for life processes. While some compounds of rhodium are carcinogenic, there are almost no reported cases of humans being affected by this element in any way. This may be because rhodium compounds are encountered so rarely. Test on plants have shown that it is the least toxic member of the platinum group of metals, according to Lenntech.
Although rhodium is generally considered non-toxic, some of its compounds are toxic and carcinogenic. Naturally occurring rhodium consists of just one stable isotope: Rh-103.
Who knew?
An alloy of rhodium-platinum is used in heart pacemakers.
South African PGM producers extract a mix of metals comprising approximately 60 percent platinum, 30 percent palladium and 10 percent rhodium, according toMining.com.
Rhodium is resistant to most acids.
Rhodium metal is rarely used by itself and almost always as an alloy.
Of the three precious metals (rhodium, platinum and palladium) currently used in vehicle catalytic converters, rhodium has by far the highest activity for the removal of nitrogen oxides (NOx) from the exhaust. It also has very high activity for the oxidation of hydrocarbons (HC) and carbon monoxide (CO) and very good resistance to the poisons present in the exhaust stream, according to Eastern Catalytic. Its primary drawback, however, is its high cost.
All rhodium compounds are easily reduced or decomposed through heating to create powdered (or sponge) metal.
Mining
Commercial rhodium is generally obtained as a byproduct of copper and nickel refining. In nature, rhodium can occur uncombined or with other platinum minerals. It can be found in river sands in North and South America and in copper-nickel sulfide ores in Ontario, Canada, according to the Royal Society of Chemistry.
Due to its rarity, the small market size and the concentrated supply — South Africa alone produces roughly 80 percent of the world's rhodium — prices are typically volatile, according to Mining.com. For example, rhodium briefly reached $10,025 an ounce just before the 2008 financial crisis hit, but then plunged 90 percent before the end of the year. In 2017, the price of rhodium more than doubled, adding $1,000 an ounce since hitting 12-year-lows mid-2016.
Storing the sun's energy
Although rhodium seems to have found a solid industry niche in cleaning car exhausts, many new research projects are showing that the precious metal may hold much more potential, particularly in its primary role as a catalyst.
In one such study, Swiss researchers at the Paul Scherrer Institute (PSI) and the ETH Zurich developed a new chemical process that uses the sun's thermal energy to convert carbon dioxide and water into high energy fuels. This chemical process involves a new material combination of cerium oxide and small amounts of rhodium as a catalyst. Their discovery is a major step toward the chemical storage of solar energy (which has been a very tricky problem for scientists). Their new findings are published in the journal Energy and Environmental Science.
Additional resources
Los Alamos National Laboratory: Rhodium
Jefferson Lab: The Element Rhodium
Royal Society of Chemistry: Rhodium
MORE ABOUT...
What Was the Black Death?
Pneumonia: Causes, Symptoms and Treatment
SEE MORE RELATED
LATEST
Why Do People Have Different Personalities?
SEE MORE LATEST
Doctors Find Bizarre Mass of Bone, Teeth & Hair in Teen's Stomach. It Was Her Own Twin.
A large lump in a teenager's stomach turned out to be her own "twin" growing inside her.
Livescience
There Are Thousands of Tardigrades on the Moon. Now What?
What might it mean for the moon to have thousands of tardigrades as new inhabitants?
Livescience
Battle-Scarred Viking Shield-Maiden Gets Facial Reconstruction for First Time
Scientists reconstructed the face of a battle-scarred Viking shield-maiden for the first time ever.
Livescience
The Mysterious 'Tully Monster' Just Got More Mysterious
Scientists reveal more mysteries about the bizarre Tully Monster, an ancient sea creature with stalked eyes that has defied classification.
Livescience
What's Inside a Black Hole?
You're about to take a dip into the inky blackness of a giant black hole and see what's on the other side of that enigmatic event horizon. What will you find inside? Read on, brave explorer.
Livescience
MOST POPULAR
Albert Einstein: The Life of a Brilliant Physicist
By Adam MannDecember 05, 2019
READ MORE
What Is the Hubble Constant?
By Adam MannDecember 03, 2019
READ MORE
What Is St. Elmo's Fire?
By Charlie WoodNovember 26, 2019
READ MORE
Phi: The Golden Ratio
By Adam MannNovember 25, 2019
READ MORE
Malaria: Causes, Symptoms & Treatment
By Cari NierenbergNovember 20, 2019
READ MORE
Meningitis: Causes, Symptoms & Treatment
By Cari NierenbergNovember 19, 2019
READ MORE
Mesopotamia: The Land Between Two Rivers
By Owen JarusNovember 18, 2019
READ MORE
The Moon: Our Planet's Constant Companion
By Adam MannNovember 15, 2019
READ MORE
Ants: From the Cool to the Creepy
By Rachel RossNovember 13, 2019
READ MORE
The Vagus Nerve: Your Body's Communication Superhighway
By Katherine GouldNovember 12, 2019
READ MORE
What If the Berlin Wall Had Not Fallen in 1989?
By All About HistoryNovember 09, 2019
READ MORE
Deforestation: Facts, Causes & Effects
By Sarah DerouinNovember 06, 2019
READ MORE
There's Something Strange Going On Inside Neptune
By David Crookes, All About Space magazine November 04, 2019
READ MORE
SIGN UP FOR E-MAIL NEWSLETTERS
Get breaking science news on monster snakes and dinosaurs, aliens, spooky particles and more!
No spam, we promise. You can unsubscribe at any time and we'll never share your details without your permission.
MOST READ
MOST SHARED
1
Extraterrestrial Mineral Never Before Seen on Earth Found Inside a Famous Meteorite
2
A Dark River Nearly 1,000 Miles Long May Be Flowing Beneath Greenland's Ice
3
Dazzling 'Temple of Colored Marbles' Honoring Roman God Discovered in Italy
4
Huge New Storm Creates Hexagon at Jupiter's South Pole
5
Scientists Found the Deepest Land on Earth Hiding Beneath Antarctica's Ice
Live Science is part of Future US Inc, an international media group and leading digital publisher. Visit our corporate site.
Terms and conditions
Privacy policy
Cookies policy
Accessibility Statement
Topics
© Future US, Inc. 11 West 42nd Street, 15th Floor, New York, NY 10036.
-
- Posts: 1355
- Joined: Wed Dec 28, 2016 10:56 am
Re: What happens if China restricts rare earths supply ?
The BigP is an idiot. All the dumb fool is doing is copying me but he doesn't have the remotest clue what he is copying.
He has lost his Oracle status big time.
Over on the other place there are a couple of idiots like him.
Mother Orchid needs to discipline him about his illegal SPAMMING.
He has lost his Oracle status big time.
Over on the other place there are a couple of idiots like him.
Mother Orchid needs to discipline him about his illegal SPAMMING.
- Black Orchid
- Posts: 26026
- Joined: Sun Sep 25, 2011 1:10 am
Re: What happens if China restricts rare earths supply ?
Mother Orchid says quit the crap 

Who is online
Users browsing this forum: No registered users and 13 guests